Laminating flexible materials - Lamination for flexible packaging | KYMC
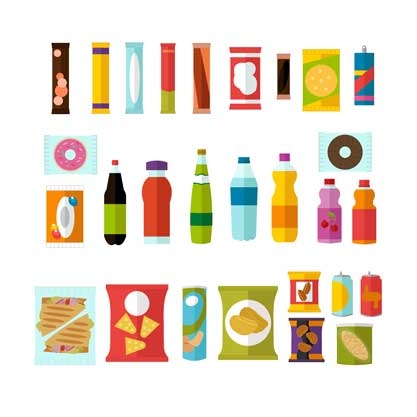
Laminating Process
Web lamination is the process where two or more flexible packaging webs are joined together through a bonding agent. Common web materials include the different types of films such as PE, PET, PP…etc., aluminum foil, and paper. Depending on the properties that one would like to achieve in the final flexible packaging, different combinations of web lamination are possible. The lamination can be between different films, between films and aluminum, between paper and aluminum, and between films and paper. The bonding agents can be in different forms such as liquid, molten state, and solid. Some bonding agent requires drying and some don’t. Some bonding agent goes through a chemical reaction while others are joined through pressure from heated rollers. In general, the bonding agent is applied to the less absorbent substrate and the second substrate is pressed against the first to produce duplex, triplex or multi-layer lamination for flexible packaging.
Applications
The goal of the laminating process is to produce a final substrate with enhanced barrier properties, appearance, and strength for flexible packaging. The different films, paper, and aluminum foil all have different properties. Some films have high dyne levels which makes it suitable for print, some films have a good sealing property which makes it suitable for becoming the most inner layer of the packaging, aluminum is known for its air-blocking barrier property, and paper is known for its porous structure that is suitable for water-based inks. At the end of the day, the choice of the laminating process is directed by the end-use of the flexible packaging product. The lamination applications are applied in many different industries, ranging from food, beverage, sanitary, medical to the high-tech sector. Wherever flexible packaging is required, there will be lamination.
Laminating machinery and laminating types
Laminating machinery can be categorized into 4 main categories by its process. This includes dry lamination, wet lamination, solventless lamination and wax or hotmelt lamination.
Dry lamination: in dry lamination, the bonding agent is first dissolved into a liquid state, then applied to one of the webs through rollers. The web with the applied bonding agent then goes through a drying process where the bonding agent dries to a solid-state. Finally, the web with the applied solid bonding agent is joined to another web through strong pressure using heated rollers. The dry lamination is the most common lamination process on the market. Commonly used to work on various film and foil substrate combinations such as film on film, film on foil, and film on paper. The advantage of dry lamination includes a wide product range, high resistance to the chemical medium erosion, and available for tough packaging condition requirement
Wet lamination: in wet laminating the bonding agent is still in a liquid state when the webs are joined together. The wet laminating process is suitable for various kinds of paper product applications. The available applications include paper on fiber, paper on paper, paper on paper board, paper on foil. The advantage of wet Lamination is a low running cost, high production capacity, and low machine investment.
Solventless lamination: solventless lamination refers to the lamination where the bonding agent is absent of solvent. The bonding agent is composed of two or more components that go through a chemical reaction with each other and therefore not requiring drying. As solventless lamination does not require drying nor does it contain solvents, this makes the solventless lamination an eco-friendly process.
Wax or hotmelt lamination: This is where the bonding agent is wax or hotmelt and is applied as a molten state onto one of the two substrates. This type of lamination is usually between paper and paper lamination or between paper and aluminum foil. This type of lamination is widely found in biscuits and bakery packaging.
KYMC expertise and knowledge
KYMC provides the widest range of lamination solutions. Whether you are looking for a laminator as a standalone or as an in-line process, we have the solution for you. On top, with our expertise and experience in the flexo printing area enables us to provide a total solution to you.
Article by Daywey Chen, KYMC