Revolutionizing Printing: The Power of Smart Production Monitoring Systems
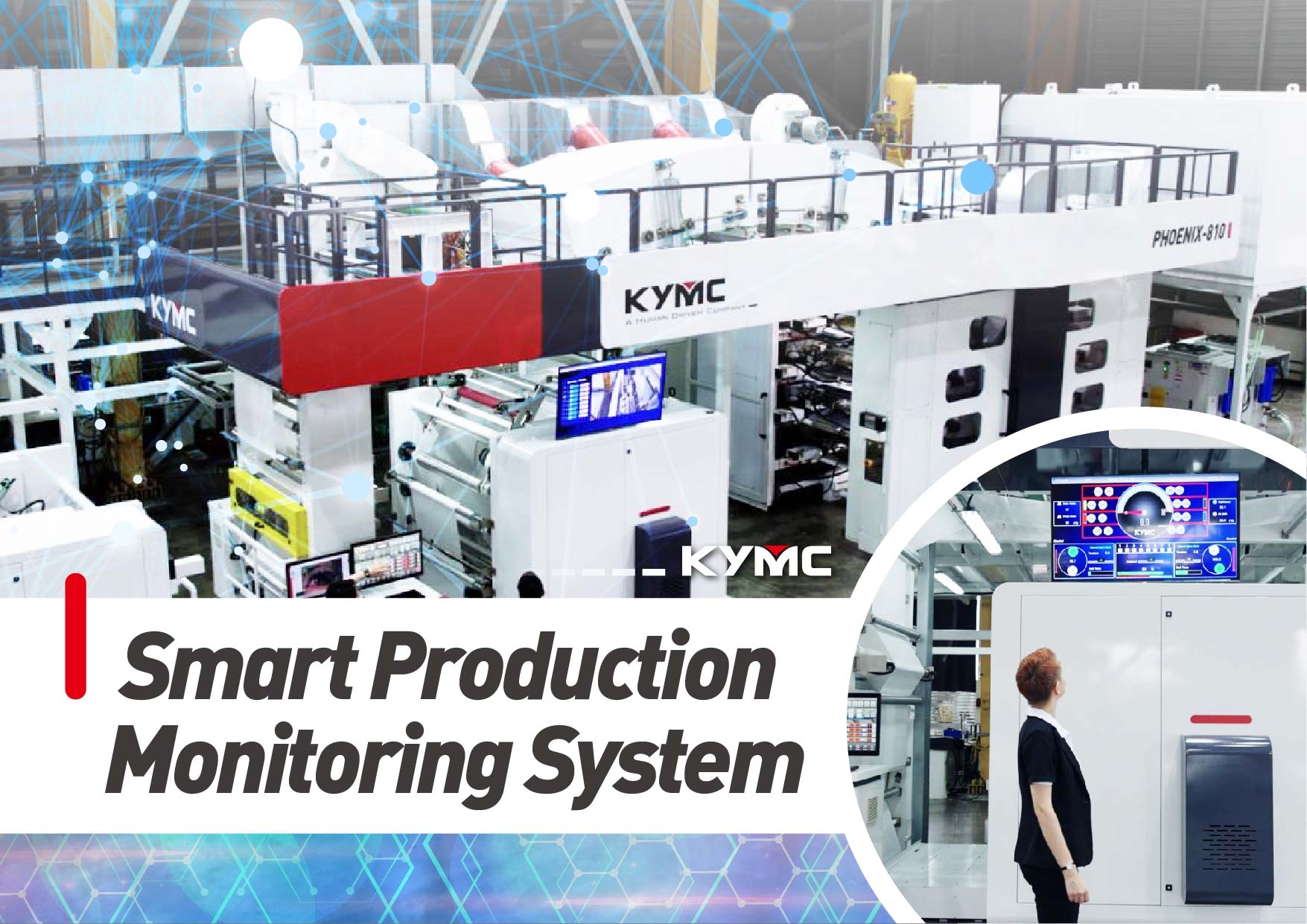
An upgrade to an ergonomic press design can turn into a more efficient production process. This is critical in a fast-paced world of printing and converting, where productivity and flexibility make all the difference. A digital kanban system for monitoring and managing the operation can contribute greatly to an ergonomics process. To be able to centrally monitor the real-time production status at the different press locations prevents unnecessary waste caused by walking back and forth around the machine. Walking back and forth to obtain status info at the different stations can be prevented. As a result, an improved ergonomic friendliness for the operator and at the same time reduced unnecessary time spent on gathering data.
Real-Time Monitoring for Enhanced Supervision:
Digital Kanban Systems provide operators and executives with instant access to production status and job information across stations located at different areas of the press. To bring back information including print job info, print setup, ink status and auto splicing status to a central monitor. Operators and supervisors can effortlessly oversee operations. This real-time visibility enables proactive decision-making, allowing for swift adjustments to printing setups, ink management, and auto splicing as needed to maintain optimal efficiency. When multiple production lines are running simultaneously, the digital kanban system will make supervision much easier and much more efficient.
Home page of the central monitor
Comprehensive Production Analysis for Informed Decision-Making:
Beyond real-time monitoring, these systems offer robust production analysis capabilities, including tracking the Overall Equipment Effectiveness (OEE). To provide critical data such as utilization rate, daily output, quantity of quality outputs, and other key performance metrics. By compiling this data into customizable reports, printers and converters can gain valuable insights into production trends and performance drivers. This data-driven approach empowers managers to identify areas for improvement, optimize resource allocation, and drive continuous process optimization initiatives. At the end of the day, helps to achieve productivity increase, cost reduction, quality enhancement, and greater capacity.
OEE report
Live View That Enables Immediate Adjustments for Critical Processes:
During auto splicing and auto wash cycles, live view capabilities provided by Digital Kanban Systems enable operators to manage and adjust the process in real-time when needed. This live feed is complemented by advanced ink supply controls, allowing for precise adjustments to the ink viscosity and temperature to ensure optimal print quality and performance. By integrating these features into a single, intuitive interface, operators can effectively manage printing processes with greater accuracy and efficiency.
Live view for splicing operation
Flexibility, Efficiency and Safety Through Wireless Control:
The adoption of industrial standard tablet computers for wireless control represents a significant advancement in printing operations. By eliminating the need for cumbersome wired connections, operators gain greater flexibility in maneuvering around the production floor while maintaining full control over printing processes. This wireless functionality not only enhances operator mobility but also provides operator real-time data and status updates on the press. This helps in identifying patterns, trends, and potential optimization opportunities.
Digital Kanban Systems are transforming printing operations by providing operators and executives with a comprehensive solution for monitoring, analysis, and control. From real-time monitoring of the production status, ink status and auto splicing status, these systems offer a holistic approach to optimizing printing processes. By harnessing the power of digital technology and data analytics, printers and converters can achieve new levels of efficiency, flexibility, and quality in their printing operations, driving greater competitiveness and success in the marketplace.