Water Based Ink V.S Solvent Based Ink
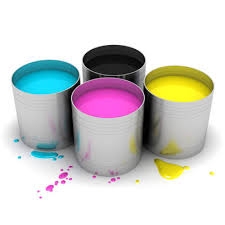
Have I Made The Right Choice?
The increase of environmental concerns and the increase of awareness in sustainability has drawn more attention to the usage of water-based ink usage in the flexographic printing and packaging industry. The two different types of ink both have its pros and cons depending on your application and needs. In this article, we lay out some of the comparison factors for you. To let you be the judge of which ink better suit your needs.
Component
So, what defines an ink as water-based and what defines an ink as solvent based? To begin with, the general composition of an ink consists of pigments, resins, solvents and addictive. This formula will generally be the same no matter which type of ink it is. Water-based ink, in general, is different from the solvent based ink by replacing the organic solvent with water. The general composition of the two different ink is shown in figure 1 below.
Figure 1
Attributes
By replacing most of the organic solvent with water will cause the water-based ink to display many of the water properties which include:
- Higher energy needed for evaporation: on average it takes 2~3 times as much energy to evaporate water than to evaporate the organic solvent
- Slower drying rate: on average water dry at 1/5 of the organic solved drying rate
- Less lubrication capability: water has less lubrication effect than organic solvent as result reducing the lifespan of flexo plate and anilox rollers.
Performance on the different substrate
The printed substrate at a high level could be categorized into absorbent and non-absorbent. In packaging, absorbent substrate commonly refers to materials such as paper and cardboard. Non-absorbent substrates refer to films such as PE, LDPE, BOPP, PET, CPP…etc. The challenge for water-based ink is simply the time needed for the ink to dry on non-absorbent substrates as it takes more energy and more time to dry. However, on an absorbent substrate where the surface tension is much higher than non-absorbent, could withstand a higher temperature and has a higher permeability, drying is less of a problem for water-based ink.
Cost Analysis
From the environmental standpoint, water-based ink emits much less VOCs. Therefore, the cost related to pollution emission is much less when compared to solvent-based ink. For instance, the cost of pollution emission permits, the cost per unit of pollution emission, and the cost of waste management such as the catalytic converters needed for VOC combustion breaking down the harmful particles. From a safety standpoint, the cost of solvent-based ink storage is higher than water-based ink, as it is more flammable, therefore more prone to explosion and fire. When it comes to prevention of work environment hazard, the is safer water-based ink is priceless.
Conclusion
Typically speaking water-based ink could be considered if your application is to run at slower printing speed and on an absorbent substrate. The water-based ink that consists of much less organic solvent could provide printers with less VOC emission issues to worry about. At KYMC we had a customer that ran solely on water-based ink as VOC emission permits are required in the region. As the sales orders fluctuate from month to month, the VOC emission permit may be insufficient or excessive depending on the order quantity of that month. To avoid this issue, this customer went 100% water based.
There are many factors to consider when it comes to ink selection, for example, machine speed, order quantity, job length, substrate, regulations, operator skill level, market demand…etc. At the end of the day choose what makes sense to you, because what makes sense to others may not make sense to you.
Source
Sun Chemical, Exploring The Pros and Cons of Water and Solvent Based Inks for Flexo Printing
Relevant Reading
Meet Ultraflex, the C.I. UV LED hybrid
Article by Daywey Chen, KYMC