How Controlling of The Water Based Ink Temperature Could Eliminate Ink Foams from Developing at The Containment Blade
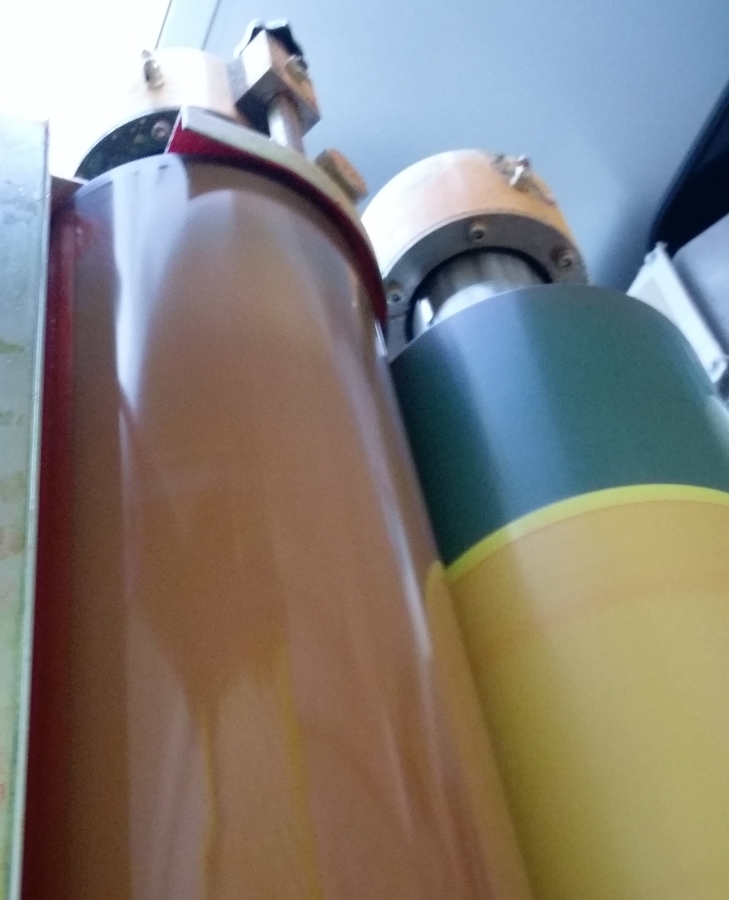
Figure 1
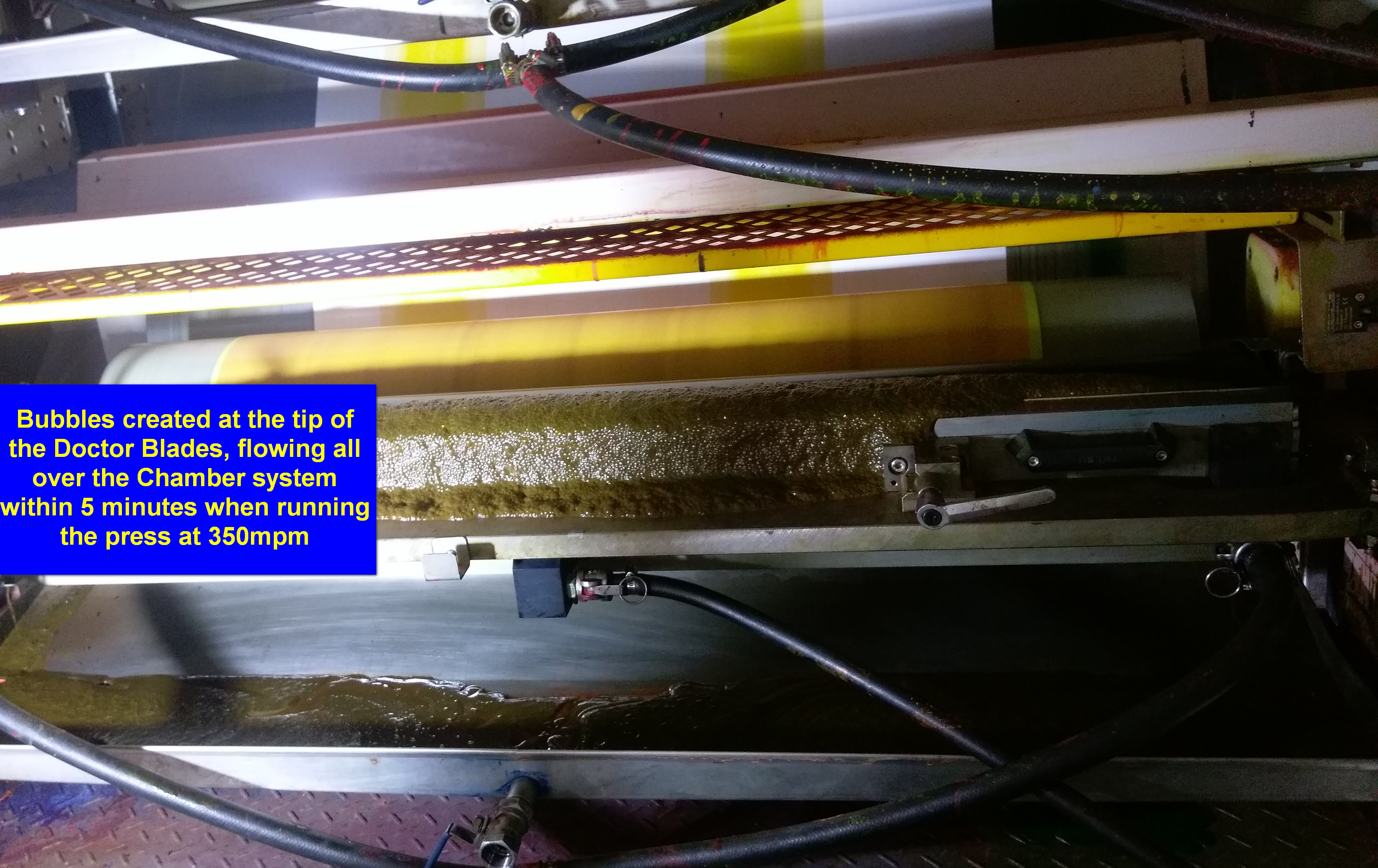
After detail analysis by the team, it was concluded that the main issue was due to the high back blade (reverse blade) pressure. During printing as air travels back into the chamber after the ink transfer onto the printing plate, if the blade pressure to anilox roller is too high, this will prevent the air and ink from reentering into the chamber. This will cause an imbalance of air and ink flow, leading to foam generation and buildup at the back blade. To solve this issue, we switched the original steel blade on the press over to a plastic blade. The new plastic blade had a larger surface area and is much more flexible than the steel blade. This change lowered the blade pressure and therefore balanced the air and ink flow, allowing air and ink to flow back to the chamber much more easily without blockage.
Another factor that we adjusted was the ink temperature. During the printing process, we found the ink temperature rose up to 32℃. For flexo water based ink, the optimal working temperature should range between 22℃ to 24℃. When the ink temperature rose up to 32℃, the pH dropped, causing the ink viscosity to increase. With the higher viscosity, air bubbles within the water based inks were harder to eliminate, especially under high press speed. To improve this condition, we used the temporary cooling device to chill down the ink temperature, helping to reduce the foam from building up during high press speed.
The result was an elimination of foams and ink spills at the chamber system after the blade switch and temperature control as shown in Figure 2.
Figure 2
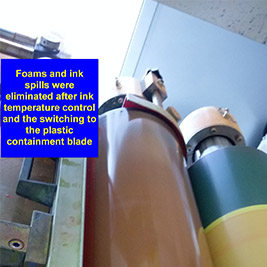
Company / Print Job Background
- Food packaging, pet food packaging, food wrappers, industrial packaging, paper bags printing and production
- Location: Central America
- Flexographic Central Impression printing
- Wide web flexible packaging application (400mm~1000mm)
- Water based ink
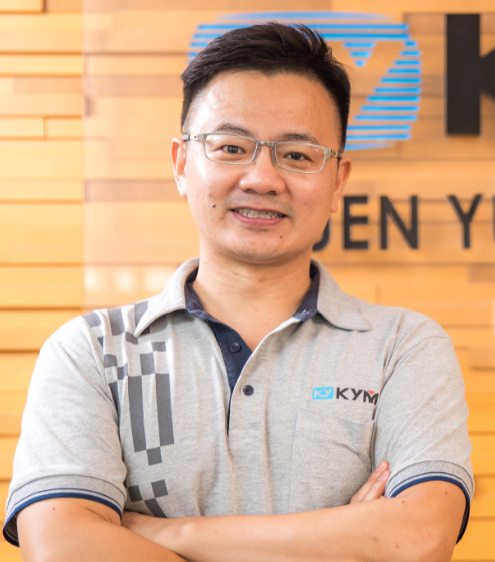
Contributed by Ivan Lin, KYMC