Different Plate Making Process Discussed Inside Out
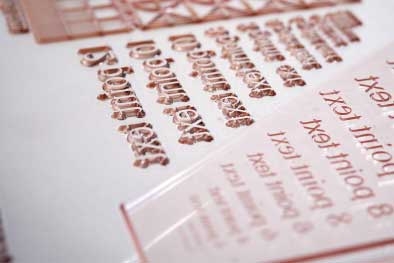
As the society lean towards more environmentally friendly production solutions. The plate making industry searches for a greener plate making process. Let’s compare some of the plate making processes.
Comparison Chart of the different plate making processes
Thermal Plate Making Process
The thermal plate making process utilize the melting point difference of the photopolymer plate after exposing to light to produce a flexographic plate. The area that is exposed to the light will solidify and have an increased melting point. Therefore, when the photopolymer plate is heated, the area that is not exposed to the light will melt. Then a non-woven fabric is used to wipe off the melted area to complete to plate making process.
This plate making process does not involve solvents. Minimal VOC is generated from the melted photopolymer plate during the heating process. The waste generated is mostly from the non-woven fabric and the wiped off photopolymers, which is much easier and cheaper to process when compared to VOC waste generated from solvent washing. Therefore, making the thermal plate making process greener than the solvent washing process.
Previously, there were concerns about the quality and lifespan of a thermal process made plate. However, as the technology advances, the quality of the plate in terms of the dots that the thermal process is able to generate, and the lifespan is matching the solvent washed process. The disadvantage of the thermal processed plate is the high cost. If technology is able to lower the cost of thermal plates, this process would be an ideal plate making process.
Some of the vendors that possess the technology for thermal processing plate includes Dupont’s FAST, Flint’s Xpress, and MacDermid’s LAVA.
Water Washed Plate Making Process
Water washed plate uses water instead of solvents in its plate making process. The area where the plate is not exposed to light can be wash away by water. Therefore, no VOC is produced in the process. This technology has been on the market for a while.
The concern of water washed plate is in its short lifespan, especially when working with water-based ink. In general, water washed plate is more suitable for UV ink and alcohol-based ink.
Laser Engraved Plate Making Process
Laser engraved plate uses high energy laser beam to engrave the desired pattern onto the rubber plate. This method does not require light exposure and washing. It can ben seen as the simplest way for plate making. The laser beam can carve out dots of any shape and heights with decent control.
The rubber material of the plate makes it more solvent resistant and wear resistant when compared to the photopolymer plate. Therefore, under the same condition, the lifespan of the rubber plate can be 10 times more durable than photopolymer plate.
The disadvantage of the laser engraved plate making process lies in its high production cost and low efficiency. The equipment needed to produce an laser engraved plate is very high. Even when using a high energy laser beam of 1,000 Watt, the production speed is merely around 0.5-meter square per hour. However, we do expect as technology advances with time, there will be equipment that are more efficient at lower.
Relevant Reading
Flexographic Plate - Photopolymer or Elastomer
AM Screening V.S FM Screening
Article by Sinwa Printech Group