Another Gearless Installation in Thailand
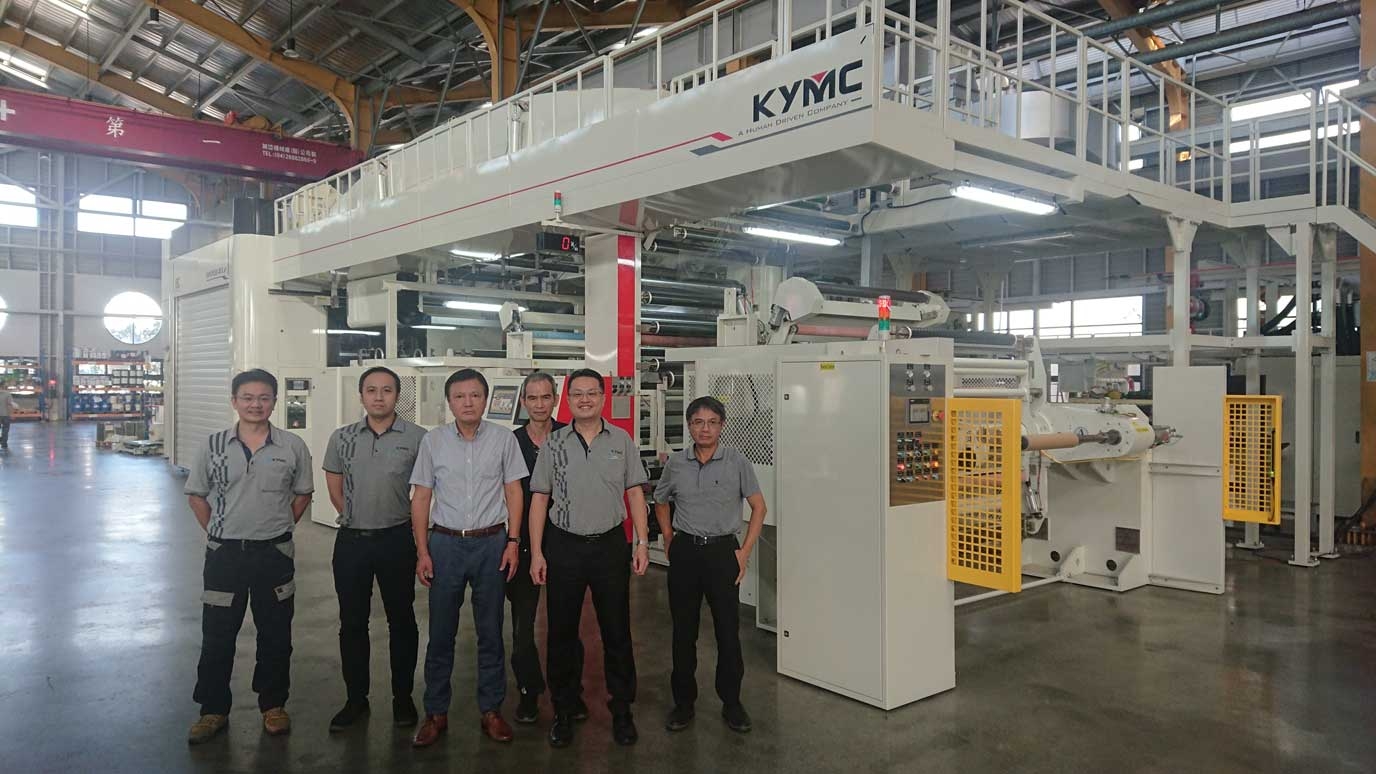
This month KYMC completed another 8 color Gearless CI Flexographic press (Euroflex) installation in Thailand. The adoption of flexographic printing for flexible packaging in Thailand had increased dramatically over the years. For this reason, the customer had decided to get into the game with an investment in a new gearless flexographic press.
KYMC’s technical capability and service capability matched the customer’s requirements. For this reason, KYMC was selected as the press supplier for the project.
Technical Capabilities
The Euroflex has a top speed of 500 meters per minute and is suitable for both film and paper on food packaging applications. Nowadays the market is demanding more flexibility from the printers and converters. Therefore, having a sufficient top running speed and the flexibility to work with different materials ensures the printer to remain market competitive.
What is the use of a top speed press without an accurate registration? With the KYMC Euroflex, the registration tolerance is controlled at +/- 0.1mm during press acceleration and deceleration. During constant speed, the registration is controlled within +/- 0.05mm. Having a tight tolerance during acceleration and deceleration is becoming more and more critical as the trend for a job run is towards a shorter one. The shorter job runs on a flexographic press can translate into more waste The waste produced during a job change. A tight tolerance during acceleration and deceleration can help to reduce this job change waste.
Trend: shorter jobs and more job changes required. Therefore, besides having a tight registration tolerance, auto splicing at the unwinder and rewinder for non-stop roll changing will certainly be beneficial. The KYMC Euroflex is able to conduct splicing under a full production speed. Moreover, the rewinder roll edge is controlled within a 1mm difference, ensuring the rolls to be workable at the downstream processes. The unwinder and rewinder have a wide tension range compatibility ensuring the capability to work with different substrates.
Some say the auto wash and auto viscosity control is a lifesaver and a game-changer.
The reason is because of the amount of human labor saving and the accuracy that it brings. inteIM (the KYMC auto wash and auto viscosity system) is an intelligent system that is integrated into the press with other press operations, and not as a standalone. All operations can be conducted under one user interface location. As a user-friendly system, additional independent monitoring and controls are also introduced at the auto wash and auto viscosity control units. With the inteIM, the ink viscosity can be controlled at +/- 0.5 sec. This is very hard to achieve with a Zahn cup measuring system plus manual ink adjustment. During auto washing, 9-10 Liters of solvent are required per color. Auto washing can be performed simultaneously at the 8 color printing stations. Therefore, taking as little as 4 -5 minutes to complete cleaning all 8 printing units. Lastly, the inteIM is a dual pump system with dynamic ink pumping pressure auto adjustment, providing a maximum stable ink supply during production.
Speaking of minimizing human intervention, the Euroflex is equipped with the auto pre-registration for a brainless registration adjustment operation. It is equipped with auto deck position control that comes with a foolproof system towards mechanical failure under the incorrect settings. Plus, a foolproof system for the plate cylinder and anilox alignment to ensure the plate cylinder and anilox are not adjusted to an angle that damages each other.
Service Capabilities
This Euroflex purchase from the customer was a second KYMC machine, one of the major reasons to select KYMC is the trust in the KYMC team and service. During the press design phase upon the customer's request, a customized amendment was made to the drying unit. To redesign the gas burner to be placed outdoor. The planning and redesign were completed within one day. As result, the customer was impressed by KYMC’s flexibility and rapid response.
KYMC stands by their customers to understand and discuss their requirements. To balance the specification needs with the equipment cost. In this particular case, the customer saw the need to save human labor in its operation. As skilled labor was not easy to find in the region. As result, the gearless CI was selected for maximum registration stability. The installation of auto pre-registration, auto deck position control and auto protective mechanism for the plate cylinder and anilox alignment to compensate for the absence of skilled labor. At the same time, auto wash and auto viscosity control were adopted so that minimum human intervention for the ink was required.