Flexography matching Rotogravure?
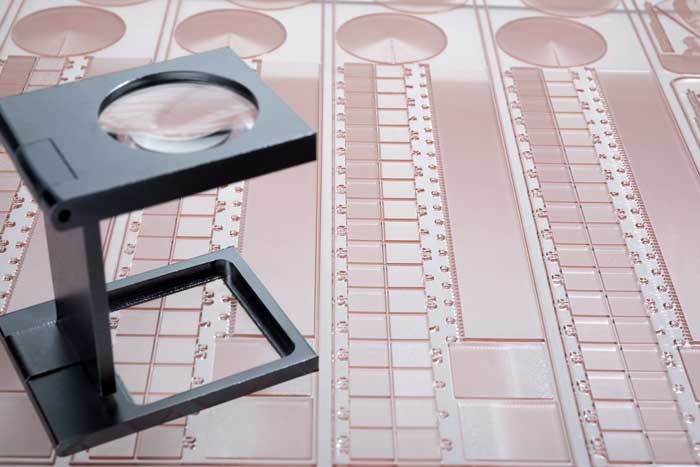
Currently, rotogravure is a more widely adopted printing process in the East. Due to environmental issues and production efficiency requirements. Many printers and converters are switching from the Rotogravure over to the Flexographic printing process. However, one of the biggest obstacles that are preventing the switch is the print quality. Rotogravure has been known to produce high quality prints easily. Traditionally, flexographic is unable to match the printing quality of the rotogravure. But as flexography matures and advances, the quality gap between the two is closing up. To produce a good quality print in flexographic printing, one must first obtain a suitable flexo plate and anilox combination. A suitable combination will allow for high quality flexographic print to match the quality of the rotogravure print.
When selecting a photopolymer plate for the flexo printing, one will need to decide on the plate’s line screen. Line screen is typically measured in LPI or line per inch. This variable indicates how many micro dots are found per inch on your plate. One can think of LPI as in pixels of a computer screen. The higher the line count, the higher the pixels. Therefore, the higher the LPI, the higher the resolution of the print.
When selecting the anilox to go with the flexo plate. There are two critical variables, which are line screen and ink volume. In this case line screen is also measured in LPI. However, instead of indicating the number of dots per inch, it indicates the number of cells per inch on the anilox. The higher the LPI, the finer the ink transfer. The other variable on the anilox is the ink volume. Ink volume is typically measured in BCM or billions of cubic microns, this variable indicates the amount of ink volume contained in a square inch on the anilox.
High line screen on the plate and anilox can produce high resolution print. It allows for highlighted areas on the image to be printed with accuracy. However, high line screen is unable to put down large ink volume that provides the fullness and richness to the image. On the other hand, a high BCM on the anilox with lower line screens can lay down more ink to provide fullness and richness to the image. However, this will reduce the resolution of the image, and is also not good for the highlight areas. It is a tradeoff between resolution and color fullness.
A commonly used line screen plate specification is 133LPI. As technologies advance, printers are going into 150LPI to produce higher resolution prints that will better match the rotogravure quality. 150LPI is less adopted before by flexo printers because of a few issues. Higher line screens cause ink blockage in the plate and cells more easily than lower line screen specifications. Higher line screen plate dots are finer and smaller. Therefore, the dots are more easily damaged. Lastly, a higher line screen comes along with less ink transfer, making images less full and less rich.
150LPI is now more widely accepted because the ink has improved over time, reducing the ink blockage issues on the plate and anilox. The plate has become more robust as the plate making process advances. Compensating for the weakness of finer plate dots on the higher LPI specification. As for the ink volume, plate imaging technologies such as pixel+, and micro screening (surface texturing) are allowing higher ink transfer on high LPI plates.
Printing technology will continue to advance, the gap between flexography and rotogravure are closing up. Feel free to contact us for more information on this topic.
Relevant Reading
Rotogravure V.S. Flexographic - Cost Analysis
Article by Daywey Chen, KYMC