4 Steps to picking out the right shape for your anilox
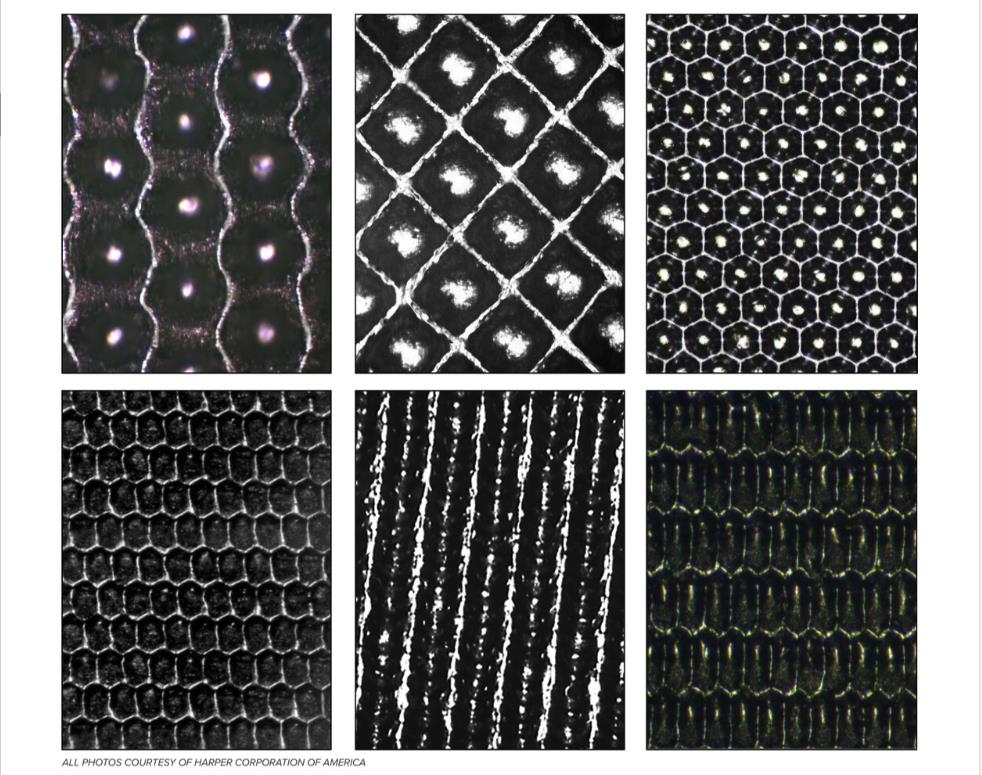
What is the right shape for my anilox? Well, this depends on what you want to print, plus various other factors like ink viscosity, ink density, ink particulates, and opacity requirements. The shape of your anilox cells will affect the amount of ink delivered to the substrate and its transfer stability.
Know your Ink
Step 1: know the ink viscosity that you will be working with
Does your ink have high viscosity or a low viscosity? If you are working with a low viscosity ink, the 60-degree hexagon cell shape will work best. The reason is that a lower viscosity ink will have a higher flow property or in other words, flow more under the same force when compared to a high viscosity ink. Therefore, more efforts need to go into containing the low viscosity ink so that the ink doesn’t flow everywhere.
The enclosed 60-degree hexagon cell will contain the ink, making the lower viscosity ink easier to control as there is less ink available to transfer. Dot gain will also decrease for the low viscosity ink with the enclosed cell.
If you are working with a high viscosity ink, channeled cell shape will be more suitable. The channel cell will allow the high viscosity ink to move through and replenish on the anilox.
Step 2: Know your ink particulates
The rule of thumb is to have your minimum cell opening to be three times larger than the size of the largest particulates in the ink. Trihelical shape cells work well with transferring particulates. Open channels work well for reducing shear in particulate ink mixtures.
Know what you would like to achieve in your print
Step 3: Know what ink density you are aiming for
Higher ink density can lead to an expansion of the color gamut and improved graphics. One way to increase the ink density is to utilize cells with greater volume so that more ink can be transferred onto the substrate. A deeper cell can help to increase the cell volume. However, there is a point of diminishing returns. Deeper cells don’t always mean more ink is transferred. A cell that is too deep can lead to ink residues at the bottom. Therefore, getting a suitable depth-to-opening ratio for your cell is important. According to Harper Corporation of America, the cell depth should be 23 ~33 percent of the cell’s opening. In special cases to increase ink density a cell depth that is 30~40 percent of the cell’s opening will be used.
Step 4: Know what opacity that you are aiming for
In general channel engraving is suitable for placing large area of white ink. The channel engraving cells will allow a better flow of the ink onto the substrate to achieve a higher opacity. However, for low viscosity white ink, a closed geometry is still preferred for the control.
Source: