UV-LED Application on Metallic Ink
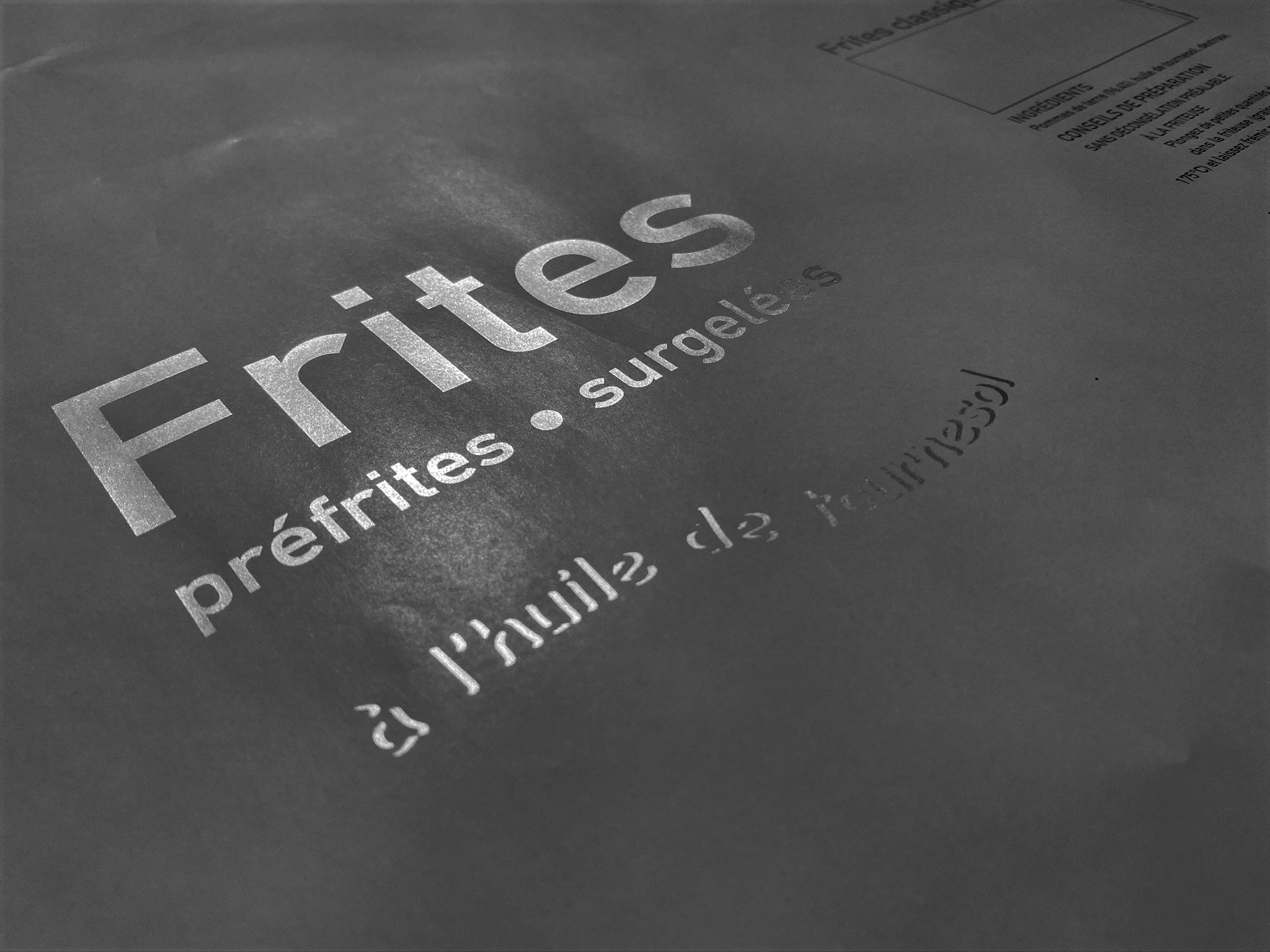
Why do printers use metallic ink?
Well, because it looks good! Metallic ink is a specialized ink that contains metals such as copper, aluminum, bronze or zinc. When the metallic ink dries, the metallic particles rise to the surface of the substrate, reflecting light to create a shine. The shinning characteristics of metallic ink have many benefits when it comes to product marketing. Metallic ink is a good way of making an impression. It helps the product stand out among the crowd, it delivers a luxurious feel, it makes the product look classier. As a result, helping the product sell and selling at a higher price.
Attempting metallic ink print job
Metallic ink should not be treated the same way as conventional process inks. It is important to understand that metallic ink will behave differently on substrates with different porous intensity. The less porous coated paper will produce a better metallic effect when compared to uncoated paper. On the uncoated paper, the ink will sink into the pores of the paper and therefore delivering less shine. It is also important to be aware that the metallic ink tends to have less rub resistance. Therefore, it is advisable to apply a protective coating on top of the metallic ink area.
The challenge of metallic ink on flexo?
It is a challenge to print metallic on flexo. Why is that? In order to produce good quality metallic print, high ink density is needed. In the flexographic process, ink is transferred from the anilox, over to the plate and from the plate over to the substrate. It takes two processes to transfer the ink from the ink chamber over to the final substrate. During each process there will be a reduction in the amount of ink transferred, affecting the final ink density. When compared to rotogravure, it only takes one process to transfer the ink from the chamber over to the final substrate on rotogravure. That’s why metallic ink usually works better on rotogravure than on flexography.
Solvent based metallic ink V.S. UV-LED metallic ink on flexo
As higher ink density will tend to produce better metallic print, this makes UV-LED ink a better choice than solvent based ink when it comes to metallic print. An important feature of UV inks are that when cured, close to the entire ink deposit will be transformed into solid. Everything you print onto substrate stays there. As for solvent based ink, the solvents within the ink will evaporate during the drying process. As the solvents evaporate, the ink deposit will continue to decrease until only the pigments and resins remain. As a result, UV-LED ink produces a higher quality metallic ink than solvent based metallic ink in most cases.
How can KYMC support our customers on the UV-LED metallic ink application?
The Ultraflex from KYMC is designed for UV-LED ink application. There is also the Ultraflex-H for those that are looking for a hybrid solution between solvent / water based & UV-LED application. The Ultraflex-H is equipped with both the conventional ink drying system and with the UV-LED curing system. The benefit of the Ultraflex-H is that printers can adopt the UV-LED units for the metallic portion of the print design and utilize the conventional units for the non-metallic portion to reduce the production cost. The Ultraflex-H is for those looking for maximum flexibility and cost reduction.