4 Common coating and lamination adhesive issues
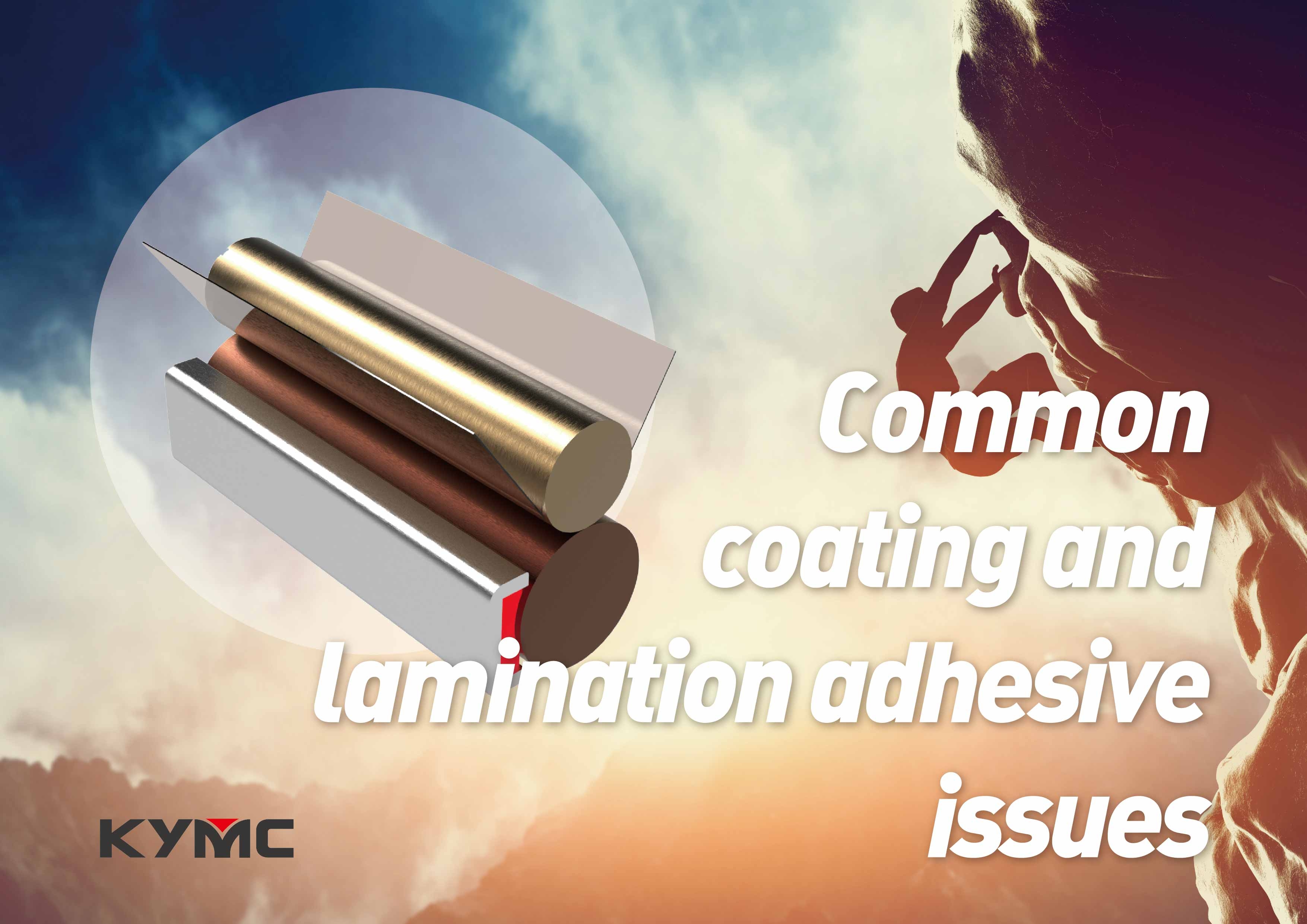
Flexible packaging is one of the most common packaging methods. The reason for flexible packaging’s popularity is due to its lightweight construction and its material savings when compared to rigid packaging. The construction of flexible packaging is the usage of laminating adhesive to bond different layers of film, foil, or paper together to form an effective structure to protect the goods within the packaging. The effectiveness of bonding and sealing of the different substrates will involve having the right adhesive mix ratio, the right coating weight, the right drying temperature and time, the right impression, and the right dyne level of the substrate. Some of the common coating and lamination adhesive issues include 1. low bonding strength 2. Tunneling in laminate 3. Bubbles in lamination 4. Ink bleed
Low Bonding Strength
The bonding strength of laminates is usually measured in Newtons. The bonding Newtons needed will be dependent on the application of the flexible packaging. A low bonding strength will cause the bonding to come apart before reaching its required Newton strength. As a result, exposing the good inside of the packaging. Low bonding strength between substrates is usually caused by insufficient adhesive coating weight, poor adhesive wetting due to insufficient surface energy of the substrate, improper temperature or impression from the nip roller, contaminated substrate surface, insufficient adhesive drying, incorrect adhesive or incorrect adhesive mix ratios.
Tunneling in laminate
Tunneling is the delamination of the substrate in certain areas of the lamination, forming a tunnel-like appearance. When tunneling appears, it is both detrimental to the appearance and packaging performance. Tunneling is often caused by the differences in moisture content in the substrates, the insufficient adhesive cure, the imbalance of web tension or improper rewind tension and taper settings, and excessive coating weights.
Bubbling in lamination
Substrates can have dust or unwanted particles on their surface which minimize the effectiveness of adhesives. Therefore, we should make sure the substrate surface is clean before laminating. Furthermore, bubbling can be caused by the lack of unwind roll tension before the substrate enters the nip. The insufficient tension will allow air to get trapped between the substrates and form bubbles. Feeding the roll too quickly can also cause bubbles therefore if this is the case, slow down the roll feeding speed into the nip before the lamination happens. Lastly, bubbles can also be caused by low nip pressure or when the nip roller is too soft.
Ink bleed
Ink bleed can happen when you start the lamination process before the ink has the chance to be fully dried. Ink bleed can also be caused by ink incompatibility with the adhesive. Not only will ink bleed cause visual defects, but it will also affect the bonding strength of the lamination. The undried ink can form a chemical reaction with the adhesive. The reaction makes a weaker bond between the substrates. Therefore, leave more time for the ink to dry before you start the lamination process.
Selecting the right combination of substrate, adhesive, and process is the key to a successful lamination. A robust lamination creates visually appealing, durable, and functional flexible packaging. When defects occur, one or more settings may need to be adjusted to solve these issues. KYMC offers over fifty years of combined experience in printing and lamination. Contact KYMC to obtain the assistance you need to maintain your dominance in the lamination market.