The guide to a perfect flexo plate
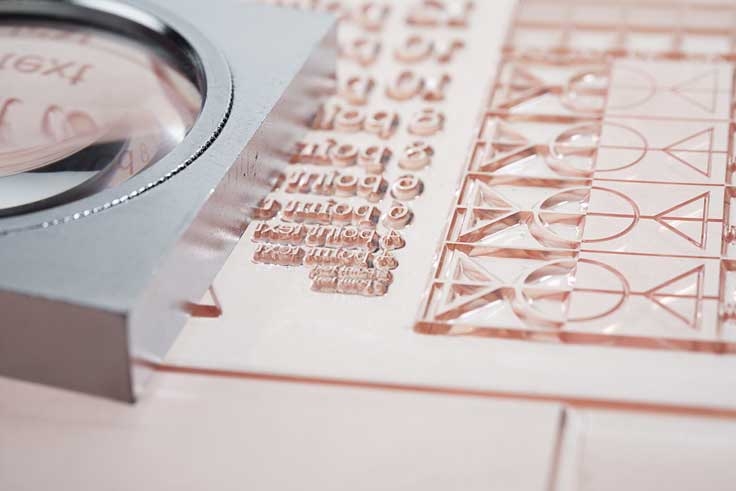
What is the definition of a perfect flexo plate? Well, this really depends on what you are going after? Are you going for the best possible image quality possible? Are you looking for the lowest cost plate? Are you looking to print images with lots of highlights? Are you looking to print images with lots of solid areas? A perfect flexo plate really depends on your requirements. In this article, we are going to look into the different metrics that you should consider when seeking and designing a flexo plate for your production. These metrics include 1. Line screen level 2. Flat top dots 3. Plate hardness 4. Plate duration 5. Micro Screening Plate 6. Plate surface tension.
Line Screen Level
With today’s technology, imaging a flexo plate with a 180LPI is achievable it enables you to produce high-definition prints with great quality in the highlighted image areas. However, it does not come without cost. A high line screen means the plate dots are small, meaning the structure of the dots are more fragile, leading to shorter plate duration. A high line screen means the gap between dots are small, meaning there are less area for the ink to flow through, leading to more ink blockage issues at the plate. One needs to balance between quality and efficiency.
Flat Top Dots
Nowadays flat top dots have almost become a must for quality prints. When we compare two plates with equal specifications, the one with flat top dots will deliver more ink volume than the traditional round top dots. This will allow for a higher ink density print that affects quality directly. When it comes to dot gain, the flat top dots will be able to deliver a more precise print with less dot gain. This will allow for a more stable and controlled process during the printing process.
Plate Hardness
In general, the softer plate has a better ink transfer capability than the harder plate. Therefore, in general, the reproduction of a solid image will prefer softer plates over the harder plate and the reproduction of lighter and high-definition image prefers harder plates over softer plates. The most commonly used measure for flexo printing plates is the Shore “A” scale. The useful range of hardness is 20 to 80 Shore A range.
Plate Duration
As good as it gets in quality, one wouldn’t want to have to remake the plate after each use. Plate duration is a very important factor to consider. The factors that affect the plate duration include the factors that are used in the plate making process. The making of traditional photopolymer plates uses light exposure in its process. Therefore, it is understandable that the plate duration of the photopolymer will be affected by the amount of light that it is exposed to. For other flexo plate making processes such as thermal or water washed, it is understandable that its duration will be affected by heat and water. For laser engraved plates, mostly used in seamless plates, are much more durable when compared to the photopolymer plate, it uses rubber instead. However, the plate cost for laser engraved plates is also much higher. Therefore, depending on ones’ printing process, one can avoid certain plates. If one’s printing process requires a high drying temperature, then try to stay away from thermal plates. If one’s printing
Micro Screening Plate
The main purpose of the micro screening plate is to increase the surface area of the dots. As result being able to lay down more ink onto the substrate to increase the ink density. Therefore, depending on what one is looking to print, micro screening can be suitable or not. Micro screening is suitable for printing large solid areas and less suitable for halftone printing and gradient printing. One disadvantage of micro screening is the plate duration. The plate duration of the micro screening plate tends to be shorter than the plate without micro screening.
Plate Surface Screening
When it comes to surface tension, the general rule is that the surface with the lower surface tension will be able to transfer the ink onto the surface with higher surface tension. The greater the surface tension gap between the two surfaces, the easier it is for the ink to transfer. In the flexo printing process. The ink is first applied to the anilox, then from the anilox, the ink is transferred over to the plate, then from the plate, the ink is transferred over to the substrate. Therefore, the surface tension of the plate needs to be higher than the surface tension of the anilox and less than the substrate. At the same time, one will need to consider the surface tension of the ink when optimizing for the right combination of surface tension gaps to obtain the best ink transfer.
Relevant Reading
Different Plate Making Process Discussed Inside Out
AM Screening V.S FM Screening
Flexographic Plate – Photopolymer or Elastomer?
Article by Daywey Chen, KYMC