Coating for Optical Films
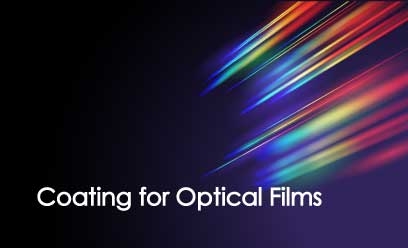
Coating is applied throughout the industry to enhance the performance of substrates. To enhance characteristics such as resistance to contaminates, durability, waterproof, conductivity, printability, downstream convertibility…etc. For optical films, coating is applied to enhance the performance of light transmission. To get the light to penetrate and to reflect off the substrate the way we wanted. To allow for a certain wavelength of light to pass through and for a certain wavelength of light to reflect off.
What is an optical film? Commercially, optical films are commonly adopted to provide shades to sunlight and UV rays, to provide display with anti-glare, to improve the contrast of the graphics, to provide the flexibility to switch between visibility and non-visibility.
An optical film usually has a multi-layer structure. Where each layer is a medium to manipulate how the light transmits through. These layers are usually a mixture of metallic and dielectric layers, all of which have different thicknesses depending on the desired properties. At the nanoscale, the difference in the refractive index between the different layers, the air between the layers and the surface of the optical component all affect the way that the light reflects, refracts, and transmits.
The fabrication of the optical films utilizes different coating techniques. Some of the common coating techniques include physical vapor deposition (PVD), and chemical vapor deposition (CVD). And roll to roll (R2R) coating.
Physical vapor deposition (PVD)
- Evaporation: a type of PVD method that involves vaporizing of solid materials in a vacuum through thermal heating, E-beam or laser then depositing that material onto the substrate. The coating created from PVD are highly durable.
- Sputter: a process that ejects particles of a solid material onto the substrate. In this process positive ions particles are injected into the chamber. The surface of a solid material is eroded by these positive ions and liberates its atoms that travel through the vacuum environment and deposit onto a substrate to form a thin coating. It is a preferred method when it comes to thin film coating.
Chemical vapor deposition (CVD)
Typically, in a CVD, the substrate is exposed to one or more volatile precursors injected into a chamber. The chamber is then heated to a reaction temperature that leads the precursor gas to react or break down into the desired coating and bond to the material surface.
The roll to roll coating process uses rolls or slot dies to place the coating materials onto the substrate. R2R coating is a much faster process when compared to PVD and CVD. There are many coating methods to choose from depending on the precision, coating thickness, coating uniformity, and coating speed requirement. Some of the common R2R coatings include direct gravure coating, reverse gravure coating, offset gravure coating, micro gravure coating, flexo coating, four roller coating, and slot die coating.
Article by Daywey Chen, KYMC