The Application of Artificial Intelligence (AI) in Flexography
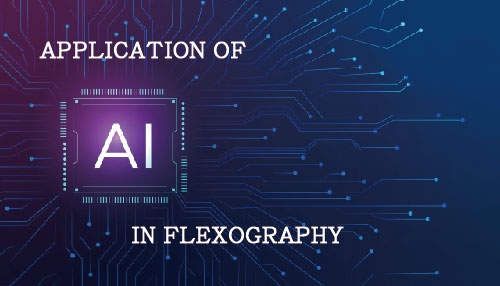
AI, Machine Learning, and Industry 4.0 have become a buzzword in recent years. But what do these buzzwords mean and how do we relate to them.? Well, we know that these buzzwords have something to do with data. Something related to data gathering and data analysis. That’s correct. In general, these buzzwords relate to, making decisions and taking actions through the support of the data collected, analyzed and modeled.
As the processing power of machines advance, the capability to collect, analyze and model data have increased dramatically over the years. This allowed a huge amount of data to be collected and at the same time be able to make sense of these data. This was not possible or not efficient enough to be carried out with the previous technologies. Now having some basic understanding of these buzzwords, this brings us to the next question. How does gathering, analyzing and modeling the data relate to the Flexographic Industry? How do I apply it to my daily production operation? In general, there are five different applications for your production. They are 1. Building production resume 2. Providing real time production monitoring 3. To optimize production continuously 4. Carrying out condition-based maintenance 5. Conducting preventive maintenance.
Building Production Resumes
With today’s computer processing power and storage capacity, all the data variables associated with the production can be collected. For instance, the tension of the web at each time period, the temperature of the rollers / ink / anilox / plate /central drum / drying oven, the humidity of the environment, the speed of the press, the vibration at different parts of the press…etc. Since all the variables are collected, when defects are found in the end products, one can go back to the production variables to identify the reasons for the defect. What went wrong? What was out of the norm?
When production variables are collected to form a comprehensive production resume. This will enable the production to be standardized. From here, to easily identify what is within the standard and what is out of the standard. When an error occurs, instead of having humans go back to test out each of the different variables to figure out what were the causes, the machine can automatically go back into the production resume and point out where the errors were in an instant.
Providing Real Time Production Monitoring
Since the data is collected in real time, it can also be monitored in real time. To monitor multiple metrics on multiple machines simultaneously on a centralized platform. This allows the managers and operators to obtain a comprehensive understanding of the production status. In an event of malfunction, production discrepancy or hazard, the system can quickly alert the necessary personnel to stop the bleeding or to prevent it beforehand.
The data collected, analyzed and modeled made the alerting system possible. The machine compares the current status against the accepted standard. When the current status falls outside of the accepted standard, an alert is sent out.
To Optimize Production Continuously
One of the big principles in the Six Sigma production process is continuous improvement. The goal is to eliminate variability and improve predictability through a data driven and statistical analysis approach. The first step into Six Sigma toward lean manufacturing is to find out where you are at! You can only begin improving by knowing where you are currently at. From here you can set goals relating to where you want to be.
The data collected and analyzed from your production history provide you with information about where you are at. For instance, what is the current OEE (Overall Equipment Effectiveness). What are the availabilities of the machines (actual production time / possible production time)? What are the performances of the machines (actual machine speed / possible machine speed)? What are the qualities of the outputs (number of good output / total output)? From here you can then set the goals that you would like to reach.
Condition Based Maintenance
To save cost and precious time is always the objective for any printers and converters. To be safe, during each maintenance, one can change all the parts that are recommended to be changed regardless of their usage or conditions. This is one way to do it. Another approach is to change only the parts that have reached a certain usage level or have worn to a certain condition. This is what we call condition based maintenance. The benefit of condition based maintenance is that you change only the parts that are necessary to change, instead of taking out both the good and bad parts together. Therefore, saving costs and reducing changing time.
To achieve condition-based maintenance. The data on the parts usage have to be collected. For instance, the amount of time that the motor had ran? At what torque? At what speed? The amount of time that the pump had operated. The amount of time that the UV-LED lamp had been turned on. At how many Watts? The number of turns that the gears had rotated. Under what temperature? When production data is collected, this production data will be compared to a library of data with information on past failure scenarios. From here deduce whether the parts should be replaced or remain in service.
Preventive Maintenance
Preventive Maintenance is an action taken before a part failure. The difference between condition maintenance and preventive maintenance is that condition based maintenance is usually carried out during a regular maintenance schedule. As for preventive maintenance, it can happen at any time. Preventive maintenance is important because I’m sure no printers or converters would like to see a production halt due to equipment failure.
Preventive maintenance can be taken during a regular maintenance schedule or when an irregular status has been detected. Irregular status such as an overheating of a certain mechanical part, an abnormal vibration of the machine, abnormal mechanical sound…etc. The data collected automatically through the sensors will enable the detection of small irregularities that are much more accurate and much more sensitive than a human detection. Therefore, finding and preventing potential breakdown sooner, mitigating the risk of a production halt.
The last thing that I want to discuss is: “Is the application of artificial intelligence (AI) in flexography for everyone?” The answer is no. Before the advent of AI, printers and converters are doing just fine. AI was never the core of printing and converting business and will not be in the future. On a scale of 1 to 10, AI will not bring a business from a 5 to a 10. However, AI can help the business to grow from an 8 to a 9, or from a 9 to a 9.5. AI can be the last millage to separate the good from the best. It serves as an enhancement to make your business better. Therefore, if your business has not established a decent foundation yet, then the adoption of AI applications can wait.
Relevant Reading
OEE (Overall Equipment Effectiveness) for Printing
5S implementation in the printing & packaging industry
Better machine communication through OPC-UA
Article by Daywey Chen, KYMC