4 Ink challenges in Flexo printing
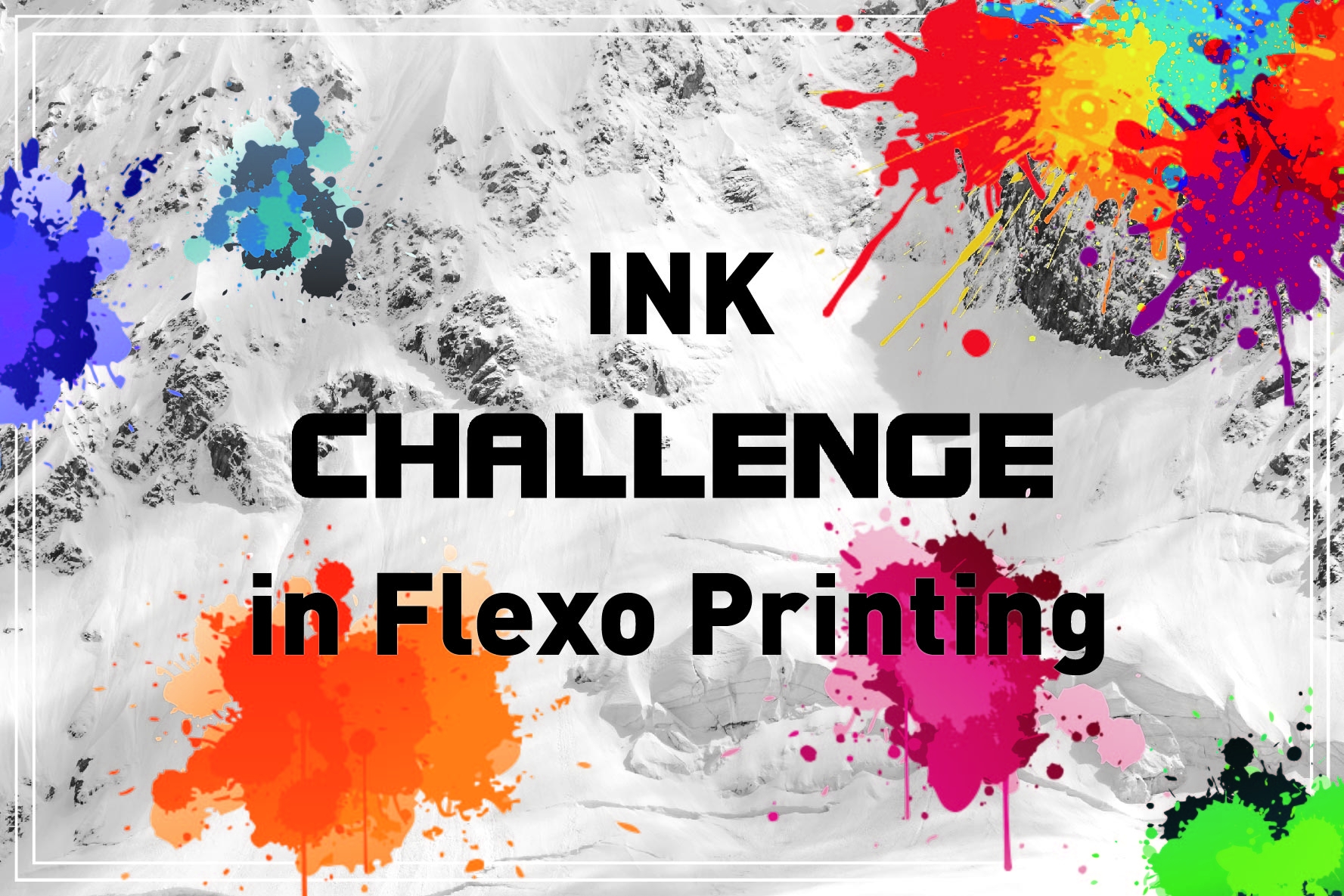
Anilox volume VS ink formulation
Over time, as the anilox volume decreases due to the ink residues in the cells, the amount of ink that the anilox is able to deliver will reduce. When the cell volume decreases by over 15 percent. In order to maintain the same print consistency, it is recommended to revise the ink formulation.
Press speed VS ink drying speed
In general, as the press speed increases, the ink will dry faster on the anilox and plate. The reason is at higher speed, the air turbulence will increase, the shear force will increase, and more heat will be generated at the anilox and plate. To decrease the ink drying speed, the energy placed into ink drying will need to be reduced to compensate for the higher airflow and higher heat generation.
Knowing that press speed will affect the ink drying. It is important to take note that the ink is formulated to match a given press speed range. Consult your ink supplier for the recommended press speed before usage.
Ink solubility VS ink stability
Ink is composed of resin that is made soluble in the solvent, then the pigment is dispersed into the resin solution to achieve the desired color. During ink formulation, solubility refers to how well the resin is dissolved into the solvent. The solubility will affect the drying speed of the ink. Therefore, it is important to obtain the right combination of resins and solvents so that you have a solubility that fits your print operation scenarios.
As the solvent evaporates and temperature builds up during printing. It is important to make adjustments by adding more solvents into the ink solution so that the ink doesn’t plug the anilox or dry up too fast on the plate. This way, with the ink stability you can achieve a consistent printing result.
Ink solvents VS photopolymer plate swelling
During printing, the ink is transferred from the anilox over to the photopolymer plate. The contact impression of the anilox and the photopolymer plate should be maintained at a minimum to prevent over-inking. Over-inking can cause excessive dot gain. Similarly, the solvent in the ink can affect the photopolymer plate’s properties to cause the plate dots to swell and grow in size or thickness. As result, leading to excessive dot gain. Some solvents have influence over the photopolymer plates more than others. For instance, alcohol has minimal influence on the plates. Glycols can create moderate issues for the photopolymer plate. Acetates will cause the plate to swell when used at high levels (> 15 percent). Therefore, it is important to understand the effect that the solvents have on your photopolymer plates before printing.
Source: Flexo (The flexographic technology source) magazine, June 2022
Relevant Reading
Ink Viscosity: Control = Efficiency
Do you have control over your ink viscosity?
Water Based Ink V.S Solvent Based Ink
Article by Daywey Chen, KYMC