Sustainable Paper Cup
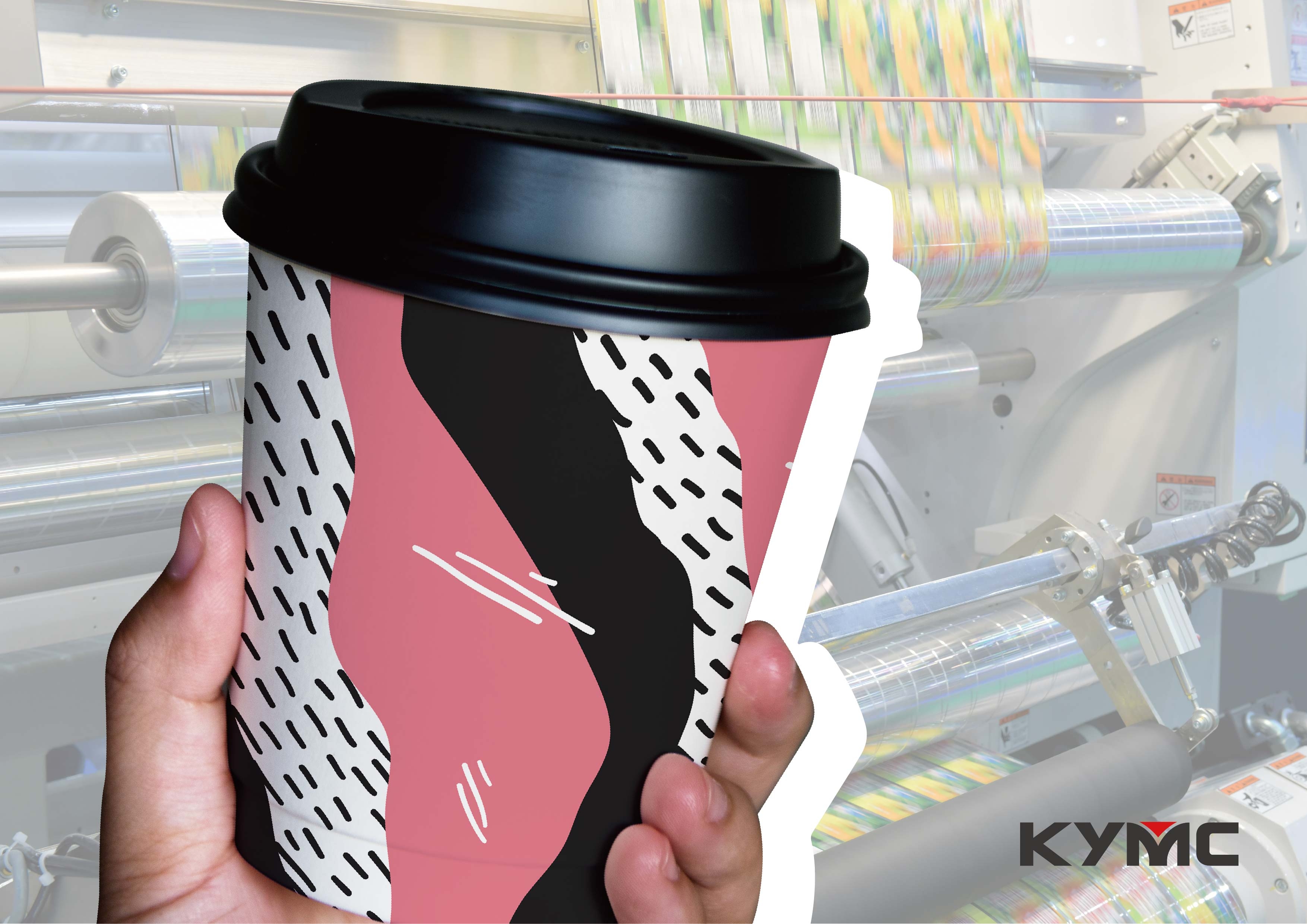
Paper cups are usually coated with a layer of plastics (Polyethylene) or wax to make them waterproof. However, this layer of plastic makes recycling much harder. As result, many paper cups ended up in the landfill. Environmental consciousness is on the rise, and companies are now seeking more sustainable paper cup solutions. Some of the solutions include using a more recyclable water-based coating, printing with water-based ink, and to use easily separable solution for plastic and paper.
Water based coating is a common replacement for PE coating. At KYMC we provide CI flexographic press for paper cup printing and attach the CI flexographic press with two downstream flexographic water-based coating units. The design is to perform front and back water-based glue coating for the paper cup after printing. The front and back registration is within +/- 1mm. The integration of the flexographic printing with the downstream flexographic coating units will increase production efficiency and lower waste production. From the past, we have seen requirement of 6 or 8 color CI servo presses at the printing width of 1,000 / 1,200mm. We have been asked by customers to integrate the CI servo press with their existing non-stop Martin unwinder / rewinder to maximize efficiency. We have been asked by our customers to integrate the CI servo press with their sealing / die cutting machines. At the end of the day, the goal is to produce sustainable paper cups at the most efficient level. KYMC is known for its capability to integrate different production processes together, to help our customers achieve their high efficiency goal.
KYMC has worked closely with a company that uses plastic injections to produce a plastic layer. Then place this plastic layer into the paper cup. To use this methodology to replace the need for PE coating. The benefit of this production process for a sustainable paper cup is the plastic layer is easily separatable from the paper cup, so that the paper and plastics can both be recycled individually.
The main trend that we are seeing on the market is to use water-based coating to replace PE coating. Not just for paper cups but for paper bags as well. The main reason that water-based coating hasn’t become the dominant process is due to the higher production cost. However, we do expect water based coated paper cups to become the dominant process in the near future as there are already many big brand owners like Starbucks and McDonalds that are adopting it. Therefore, if you are interested in replacing your existing PE coating methodology for paper cup production with a more sustainable water-based coating solution, please reach out to a KYMC representative to learn more.