5 things to look for when choosing the ink supply and washing system for your printing press
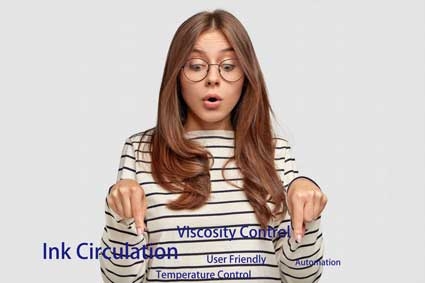
Having a stable ink supply that is maintained at the desired condition is very important as it will directly impact your print quality. We would like to see the delivery of the ink maintained at a constant speed, at a constant suitable viscosity level and at a constant suitable temperature.
The number of functions equipped into the ink supply and washing system can vary. The more function the more cost. At the end of the day, we are not trying to find the best inking system with the most function. Our goal is to find the most suitable system for your needs. Below are 5 things that you can look into to help you select your ink supply and washing system.
How are the ink circulated?
- What is the inking path like? Cleaning the inking system can be a pain in the ass when it comes to cleaning the ink pipes. Often a small amount of ink residue gets left behind in the pipe. This is especially true for solvent based ink. Over time, this will cause the pipes to decrease in its delivery volume as the ink residues blocks up portion of the pipes. This will cause your ink delivery to be less than what was expected. In general, the shorter the pipes the more stable of the system and the easier it is during cleaning.
- How are the pumps designed? Is it a motorized pump or not? Often a motorized pump can deliver a more stable ink flow. How many pumps are in the system? Is there only one pump for each color to deliver the ink from the ink tank to the ink tray on the printing deck, and letting the ink flow back to the ink tank by gravity? Or are there two pumps in the system, one for delivering the ink from the ink tank to the ink tray and one from the ink tray back to the ink tank?
- Is the inking system bi-directional? Meaning the ink can flow in two different directions. Inking system that is bi-directional are easier operationally when it comes to collecting the ink back into the ink tank to be used later on in another job.
How are the viscosity controlled by the system?
- To control the ink viscosity, the system must first be able to measure ink viscosity accurately. There are different types of sensor equipment and designs to measure the ink viscosity. Many sensors use the ink flow rate as a key measurement metric. Therefore, it is important to get the ink to flow at a constant rate when passing the sensor. When the ink flows pass the sensor, sometimes bubbles will be created (especially true in water-based ink), sometimes the waves will be generated. As result impacting the accuracy of the measurement.
How are the temperature controlled by the system?
- The temperature of the ink is usually controlled by a chiller/heating system. Where cooled water or heated water will run side by side with the ink. The cooling or heating mechanism can be designed to control each color unit individually, with this mechanism the different color stations could be set at different temperature. This kind of mechanism provides the most control over the ink temperature. Another type of design is to control all of the color units at once. The same water source will flow from the first color unit to the last color unit. Usually, this will lead to a slight temperature difference between the first color unit and the color units towards the end. Depending on your printing need, you can choose to have a separate cooling/heating system or a combined one at a lower cost.
How user-friendly is the ink system?
- Sometimes the little things can have a great impact. Are your ink supply and washing system designed in a way that is maintenance friendly? Are parts that needed replacement over time easy to change? For instance, the pipe needs replacement after a period of time. How easy is it to change the pipes, will there be additional tools that are required to make the change? Is the ink system located in a position where it is easily accessible and does not get in the way of your operator's path?
The amount of automation of the ink system
- In an auto ink supply and washing system, the amount of human efforts is dramatically reduced when compared to the manual cleaning system. The benefit of becoming automatic is the decreased in amount of dependence on people. A skilled labor may be able to change a set of inks in 20 minutes. However, it may take a novice 40 minutes, making your production line unpredictable. Automatic system helps to standardize process making your system more stable and most often faster as well. The drawback is the higher initial cost of the automatic system.