How to Choose a Flexographic Printing Plate
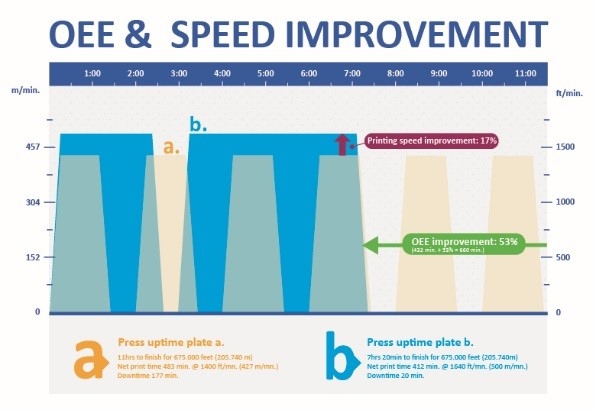
This week KYMC invited AsahiKasei to share about the factors to consider when choosing a flexographic printing plate. To draw a case study demonstrating that choosing the right plate could impact the production efficiencies in terms of printing speed and machine downtime significantly: as much as 53% in overall equipment efficiency.
How to Choose a Flexographic Printing Plate
There are many factors to take into consideration when choosing a flexographic printing plate. These include quality requirements, run length and the substrate being used, to name a few. Increasingly, both environmental impact and overall equipment efficiency at the press are also driving factors in the choice of a plate.
Gateway Packaging, based in Tennessee in the United States, is a leading high-end printer/packaging converter and the largest pet food packaging provider in North America, took all of these factors into consideration as it worked to completely revamp its platemaking department. Once the many choices in the market were narrowed down to two, Asahi Photoproducts AWPTM plates and a competitive plate, Gateway performed a production test to compare the two. The test was run on an F&K 20six flexographic press using 40-pound coated white paper and solvent inks, with a run length of 675,000 feet (205,200 meters). In testing the first set of plates, the press ran at 1,400 feet per minute (427 m/min.) with a total production time of 483 minutes or 11 hours and a total plate cleaning time of 177 minutes, as well as a requirement to clean plates every 2.5 rolls of media at 32 minutes per time.
With the Asahi plates, under the exact same conditions, Gateway was able to run the press 17% faster, at 1,640 fpm (500 m/min), and only had to stop for plate cleaning once. That stop only required cleaning two plates and took 20 minutes. The result was a total production time of 432 minutes or 7.2 hours, almost 4 hours faster and an astonishing 53% improvement in Overall Equipment Efficiency (OEE).
These achievements are enabled by Asahi’s Clean Transfer Technology, which produces a clean ink transfer and prevents ink accumulating on the plate surfaces and shoulders in screen areas. This leads to fewer cleaning intervals and reduced press downtime, as well as significant quality improvements. Precise plate register achieved with Asahi plates also ensures very high-quality process printing with a fixed color palette, minimizing the need to use and manage spot color inks.
Asahi recognizes that its AWPTM plates are not a solution for all flexographic printing and has developed a broad portfolio of plate offerings to accommodate all flexographic printing needs. To help clients make the right plate choices, Asahi has created a plate selection tool, available online at http://www.asahi-photoproducts.com/en/home#producten_link.
About Asahi Photoproducts
Asahi Photoproducts was founded in 1971 and is a subsidiary of the Asahi Kasei Corporation. Asahi Photoproducts is a leading pioneer in the development of photopolymer flexo printing plates. By creating high quality flexographic solutions and through continued innovation, the company aims at driving print forward in balance with the environment.
Follow Asahi Photoproducts on
Article By Dr. Dieter Niederstadt, Technical Marketing Manager
Asahi Photoproducts