Ink Viscosity: Control = Efficiency
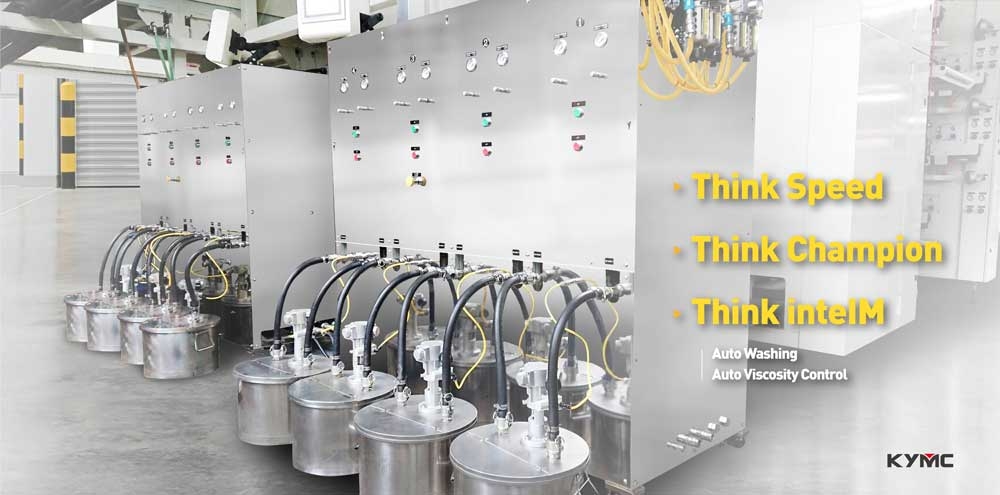
The flexographic printing presses of today are a piece of high-tech machine. This includes equipping with technologies such as 100% inspection system, auto impression, auto registration, auto edge guide, NIR drying system, industry 4.0 data collection and analytics functions…etc. However, many printers are still using the most primitive way to control one of the most important factors in flexo printing: ink viscosity. When it comes to measuring the ink viscosity. Many printers have remained holding a Zahn cup in one hand and a stopwatch in the other. To depend on one’s visual to gauge the amount of time it takes for the ink to drain from the Zahn cup.
Why is an accurate ink viscosity crucial?
[Quality]
- Consistent ink viscosity during a job run will lead to inconsistent ink layers, directly affecting the print quality.
- Ink viscosity will affect the capability of the ink to transition from anilox to plate, and from the plate onto the substrate.
- Ink viscosity will affect the ability to dry in time.
[Cost]
- Higher than needed viscosity generates unnecessary costs.
- Material waste caused by bad print.
- Labor waste caused by bad print.
- Other operational waste caused by bad print.
Control = Efficiency
Ink viscosity control can be broken down into two stages. Stage one is to accurately measure the ink viscosity, and to adjust the ink to the desired viscosity. Stage two is to maintain the ink viscosity at the desired level. Accurate measurement is only the beginning, if the viscosity cannot be maintained over the print production, what is the use of it? To be able to maintain the ink viscosity over the production period is the hardest part. Only when one is able to control the ink viscosity, one can achieve efficient print production. Otherwise, the desired print quality may not be reached, or the quality may be inconsistent. Leading to unnecessary waste, impacting the competitiveness of the business on the market.
How to effectively control the ink viscosity?
Now we understand the importance of having control over ink viscosity, which brings us to the next question. How do we do it effectively? There are three main types of measuring instruments that can help us, which are 1. Ford Cup, Zahn Cup. 2. Falling Ball Viscometer 3. Vibrational Viscometer.
[Ford Cup, Zahn Cup]
The most traditional way of measurement. To fill the cup with ink, and then measuring the time it takes (usually measured in seconds) for the ink to drain with a stopwatch. The longer it takes for the ink to drain indicates a higher viscosity, and vice versa. This method is recognized as the simplest and cheapest way for measurement. However, if we dive into the indirect cost of the time involved and the waste involved with this method. The Ford cup, Zahn cup method may be in fact the most expensive instead. How is that so? Let’s go into some of the math together.
Scenario
- 6 color print
- Printing press operating at an average 40 hours per week
Calculation
During the printing operation, due to factors like temperature and humidity, the viscosity of the ink will alter. This means that the operator will need to constantly re-measure the viscosity of the ink throughout the operation. At the same time, constantly readjusting the ink to achieve a constant viscosity. Assume that we need to measure and adjust the ink viscosity very 30 minutes. For each color, it will take 3 minutes to measure and 5 minutes to adjust. A total of 8 minutes per color. Summing it up, a total of 64 hours of manpower are needed per week. If we assume 40 hours in a workweek, this indicates that there needs to be more than one person on the ink measurement and adjustment operation. The above scenario is under the assumption of accurate measurement and adjustment. If the measurement or adjustment is off, causing more ink and material waste. This will lead to an even higher cost.
Ford cup and Zahn cup is a low tolerance instrument. It is common for the tolerance to be off by 5 to 10%, meaning for a 20-second measurement, it can be off by 1 ~ 2 seconds. Furthermore, this measuring method over relies on humans. This leads to the high variability and limited accuracy. This type of measuring method is fragmented. You measure the viscosity, then you come back to it 30 minutes later. During this time lag, the ink viscosity may have changed, therefore may have affected print quality. When you account all these factors into the Ford cup and Zahn cup measuring system, it may turn out to be the most expensive one.
[Falling Ball Viscometer]
The falling sphere viscometer drops a ball with known density and dimension into the fluid sample and measures the time it takes for the sphere to fall to a specific point. The falling ball viscometer utilizes the same measuring concept as the Ford cup or Zahn cup, which is to measure a flow under gravity. The sensors to measure the speed of the falling ball will digitalize the information gathered, therefore increasing the measurement accuracy when compared to manual measurement. However, the falling ball viscometer is still a fragmented measuring system, therefore there will be discrepancies between measurements and between adjustments. Even though there is room for improvement. Many printers find the falling ball viscometer sufficient enough.
[Vibrational Viscometer]
This is currently the most accurate ink viscosity measuring system on the market. To measure the viscosity, a vibrational viscometer measures the damping of an oscillating resonator immersed in the sample fluid. The different types of oscillating resonators include quartz crystal resonators, surface acoustic wave resonators, vibration metal rod and torsional resonators. Through the damping effect that the ink has on the resonator, the system calculates a viscosity value. This measuring method is a continuous measuring method, meaning measurements are constantly being conducted. Unlike the fragmented method of the Zahn Cup and Falling ball viscometer, there will be no time lag in-between measurements. So how accurate is this type of system? For instance, when we pour 20 grams of solvents into a 25 kg bucket of ink. Through the vibrational viscometer, it will detect a 0.1-mPa.s viscosity change. If we were to convert it into a Zahn cup unit, it will be approximately 0.02 seconds. Therefore, making this fine measurement impossible on a Zahn cup.
As technologies advance, the print speed gets faster and faster. This also implies that each mistake will be enlarged. Each mistake on the press can turn into hundreds or even thousands of meters of waste in a few minutes. To prevent and mitigate these wastes, printers have invested heavily in high-tech features. However, many have neglected the importance of ink viscosity control. Always keep in mind that only when you have control over your ink viscosity, will you be able to achieve efficient production.
Article by Daywey Chen, KYMC