All About Automation
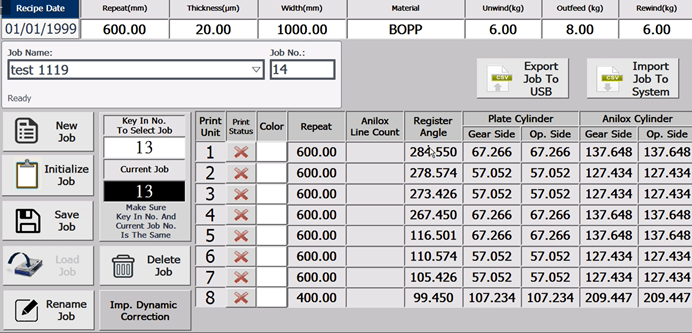
As shorter lead time is the key to success, the KYMC system is designed in many ways to help our customers achieve shorter lead time through automation. The goal of the KYMC system is to automate as much as possible and to depend on the operator as little as possible. This will allow for a faster print job time and to minimize errors caused by humans.
Auto Recall Job Recipe
The ability to automatically call up existing job specifications to expedite the setup process, without having to input the same or similar specification repeatedly.
The material specification.
Tensions at the unwind, outfeed and rewind sections.
The different repeat print lengths at the different color stations.
The register angle, plate cylinder and anilox cylinder position at the different color stations.
Export or import job specifications into and out of the system.
Auto Tension Calculator
Automatically calculate and recommend the needed tension for the job. Even a less experienced operator can set the tension specification with ease.
A recommended tension can be calculated based on the material type, material thickness and material width.
The recommended tension at the unwind, outfeed and rewind sections.
Auto Pre-Registration
To automatically set the registration before the actual production job begins, saving tons of time and material waste.
Registration can be adjusted during machine hold.
Once the production job begins, auto pre-registration kicks in, adopting the registration adjustment made during machine hold
Registration can be set in front of the controller monitor without eyes on the printing deck for the actual print.
Auto Ink Viscosity Adjustment
To automatically and continuously adjust the ink viscosity without human intervention for maximum precision.
To utilize a micro- vibrating element for sensing viscosity level, providing an accurate measurement tolerance of + 1%.
Continuous measurement, monitoring and display of the ink viscosity level and the ink temperature at the different color stations.
Auto Print Deck Cleaning
To automatically and simultaneously clean the print decks with the choice of three different cleaning modes. To achieve a hands-off operation while maintaining flexibility.
Equipped with 3 different cleaning modes, Fast, Normal, Intense.
Start your auto cleaning with one press of a button.
Different color stations can operate simultaneously either with the same cleaning mode or a different cleaning mode to maximize efficiency.
Auto Temperature Control of the Central Drum
To maintain the central drum at a constant temperature for maximum print results
Cooling units and heating units to maintain the central drum at an exact temperature during machine run and during press idle.
Auto Splicing at Winders
You never have to stop the production again due to a finished roll or a roll getting too large.
Auto unwinders with butt splicing or lap splicing capability.
Auto taper tension adjustment at the unwinder and rewinder.
Auto Dynamic Impression Adjustment
Achieve optimum print at all speeds. The impression will be automatically adjusted according to the press speed.
To increase impression during higher production speed.
To reduce impression during slower production speed.
Auto Recycling of Hot Air
To reduce carbon footprint through the automatic hot air recycling mechanism, saving energy and production cost.
Saving up to 30% in energy cost through hot air recycling.
Auto hot air recycling mechanism based on the lower explosive limit (LEL).
Safety measures based on ATAX standards.