Wide Web Flexo Press – Setup Operation
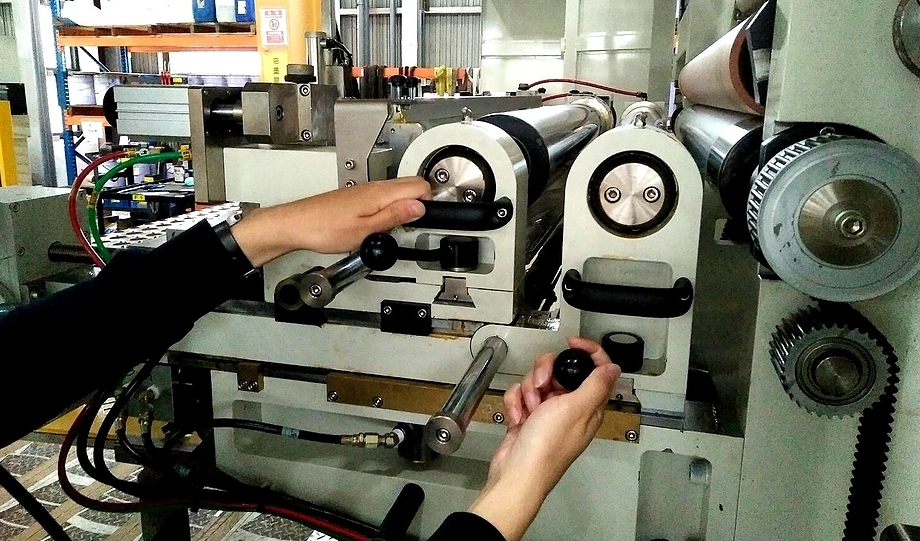
Investing in the flexographic press is the easy part. The hard part is to get the flexographic press up and running. How to get the press operational? In this article we will be discussing the main steps in setting up a wide web flexographic press.
Job Verification
To verify the job that you are about to run. To verify the job, one needs to go back and review if there are any samples that one can refer to. To look for supporting materials such as prepress proofs. To identify and plan out the number of colors needed for the job. To verify if the printing plates are defected or not and if the printing plates are mounted accurately onto the cylinders or sleeve. To confirm the substrate to be used.
Print Deck Planning
When planning for the print deck, one has to confirm if the print job is a surface print or reverse print. For paper printing, most often surface print is used. For film printing, most often reserve print is used. Reverse print on film is commonly adopted in the food packaging industry. The reverse print is to help protect the ink and to enhance the gloss of the package. When conducting surface printing, it is advised to print from the lightest to the darkest color. This order will be the opposite for reverse print.
During printing, not all the print decks will be fully used for each job. The operator needs to adjust the deck set up according to the printed image, needed colors, and upcoming jobs. Large ink coverage requires more energy for drying. When possible, skipping a few ink decks to allow for longer drying through the inter color dryings units before the next ink color is printed.
Figure 1: CI Print Deck
Selecting the Anilox and Plate
As many say, anilox is the heart of flexographic printing. The anilox can affect the end result greatly. Therefore, choosing the suitable anilox to go with the printing plate is crucial. A suitable anilox will provide a suitable amount of ink. The most common anilox used is the 60-degree engraving anilox. This engraving specification can meet the demand for most jobs. In the recent year, therefore also the GTT anilox. The GTT anilox defers from the conventional anilox by tearing down the walls between the cells to allow for more ink flow. The GTT anilox is often used for fine printing with a high line screen. According to the different jobs, different anilox will be selected. For coating and varnish, anilox rollers with a line screen between 85 to 200 (LPI) is advised. For printing solids, anilox rollers with a line screen between 200 to 400 (LPI) is advised. For half-tone printing on paper, the advisable minimum anilox to plate screen ratio is 4:1. For example when the plate screen is 100LPI, then the anilox should at least 400 LPI. For half-tone printing on film, the advisable minimum anilox to plate screen ratio is 6:1. So a plate screen of 100LPI will go with a minimum 600LPI anilox. Another decision to make when selecting the anilox is the ink volume. The ink volume of the anilox is commonly measured in BCM. A volume range of 1.6 BCM to 4 BCM is generally used for reproducing screen and process work. 3 to 7 BCM is used for printing line work. 5 to 8 BCM for solids prints. Higher BCM anilox should be used during coating or varnish applications.
Figure 2: Recommended Anilox Line Screen to Volume Combination
Doctor Blade Setup
The doctor blade will scrape off the excess ink from the surface of the anilox. The doctor blade should touch the anilox at the minimum required pressure. A pressure that is too high can lead to anilox scoring, damaging the anilox.
Figure 3: (left) Suitable Pressure (right) Pressure Too High
Ink pH and Viscosity Setup
Before printing, one should understand the attributes of the different inks. For example, the suitable pH range, the suitable viscosity rage, the solvents and the addictive to add or reduce for ink adjustments.
In terms of ink viscosity level, higher viscosity will tend to produce darker print results, lower viscosity produces lighter print results. During printing, as the solvents or water evaporates into the air, the viscosity of the ink will continue to increase. Therefore, to maintain the same viscosity level, one will need to add additional solvents or water into the ink. As solvents evaporate much faster when compared to water. It is advisable to check for the ink viscosity every 10 to 15 minutes for solvent-based ink and 30 minutes for water-based ink. When adjusting for the viscosity, one should also keep track of the pH level. For example, adding water to the ink will reduce the viscosity. However, it will also reduce the pH level. Therefore, additives like amine are introduced at the same time during ink adjustment to maintain a constant pH level.
Ensure Sufficient Dyne Level
In order for a good ink transfer to the substrate, the substrate needs to have a dyne level greater than the ink. Solvent-based ink’s dyne level usually falls around 23 dyne level and water-based ink usually fall around 30 dyne level or higher. It is recommended for the substrate to have a dyne level approximately 10 levels higher than the ink being used. The substrate can be treated to increase its dyne level. However, the increased dyne level is not permanent but will decrease with time. Therefore, before each print, always check for the substrates' dyne level.
Figure 4 : (left) Low Substrate Surface Energy (right) High Substrate Surface Energy
Other Pressrun Checks
- Listen for unusual press noise. This may indicate mechanical issues.
- Be aware of the roll diameter at the unwind and rewind. Set alerts when the unwind roll is about to finish
- Constantly monitor the video camera image for any defect in printing
- Monitor any changes in the substrate tension at the different part of the press
- Monitor any changes in the temperature at the print decks
Article by Daywey Chen, KYMC