Flexographic Plate – Photopolymer or Elastomer?
April 20, 2018 | Daywey Chen
2018-07-19
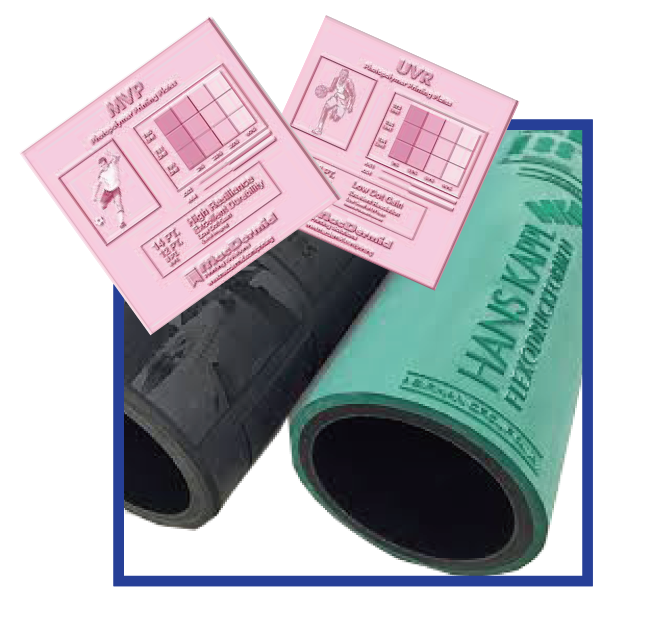
How to choose between photopolymer plate and Elastomer plate
There is no such thing as the best selection when it comes to Flexographic plate material and therefore the process to adopt. Different plate material has its own advantages and disadvantages, therefore, choose the solution that best suits your needs. If I may draw an analogy, a Ferrari is no doubt an excellent car, but if your travel plan is to get from Asia to North America then your most suitable tool would be an airplane instead. Likewise, for Flexographic printing it’s about finding the most suitable solution depending on that your goals are.
At KYMC we have observed the integration of the elastomer plate and photopolymer plate usage. Taking advantage of each strength. The more durable and seamless attributes of the elastomer plate are used for printing repeated background designs. The fragmented designs and designs that require many versions are printed using photopolymer plates.
Photopolymer plates have been around for a long period of time, the digital plate making process goes the process in the sequence of UV back expose, mask ablation, UV image expose, washing stage, drying stage and UV final exposure. There are many processing stages and takes up much time.
Elastomer plates making process involves the direct engraving of the design onto the rubber material. The major distinction between the photopolymer plate making and elastomer plate direct engraving is the absence of the plate exposure and the washout process for the elastomer plate. The needless of the solvent wash out process lead some to say that the elastomer plate is a more environmentally friendly solution. Some say the fewer steps required for elastomer plate making leads to a higher product quality: less room for errors at the different stages. The process includes laser engraving, water wash and dry, that’s it!
The elastomer plates didn’t make it to the mainstream until recently because back then the plates are averaging at a screen value of 85lpi, nowadays 200lpi line screen elastomer plates are widely seen on the market. Back in the days, the low screening of the elastomer plates caused it to be used mainly for the printing of uncomplex repeating background designs on tissue, wallpaper and other materials for the decorative market. In general elastomer plates are more durable than photopolymer sleeve in terms of scratch resistance, heat resistance and the ability stand up to solvent inks. The longer production life eliminates the need to purchase more plates for long runs and repeated jobs.
At the end of the day, choose the plate according to what you would like to accomplish. There are many vendors on the market to choose from, choose your vendors wisely as the capability of different vendors may vary.
Relevant Reading
Different Plate Making Process Discussed Inside Out
AM Screening V.S FM Screening

Article by Daywey Chen, KYMC
There is no such thing as the best selection when it comes to Flexographic plate material and therefore the process to adopt. Different plate material has its own advantages and disadvantages, therefore, choose the solution that best suits your needs. If I may draw an analogy, a Ferrari is no doubt an excellent car, but if your travel plan is to get from Asia to North America then your most suitable tool would be an airplane instead. Likewise, for Flexographic printing it’s about finding the most suitable solution depending on that your goals are.
At KYMC we have observed the integration of the elastomer plate and photopolymer plate usage. Taking advantage of each strength. The more durable and seamless attributes of the elastomer plate are used for printing repeated background designs. The fragmented designs and designs that require many versions are printed using photopolymer plates.
Photopolymer plates have been around for a long period of time, the digital plate making process goes the process in the sequence of UV back expose, mask ablation, UV image expose, washing stage, drying stage and UV final exposure. There are many processing stages and takes up much time.
Elastomer plates making process involves the direct engraving of the design onto the rubber material. The major distinction between the photopolymer plate making and elastomer plate direct engraving is the absence of the plate exposure and the washout process for the elastomer plate. The needless of the solvent wash out process lead some to say that the elastomer plate is a more environmentally friendly solution. Some say the fewer steps required for elastomer plate making leads to a higher product quality: less room for errors at the different stages. The process includes laser engraving, water wash and dry, that’s it!
The elastomer plates didn’t make it to the mainstream until recently because back then the plates are averaging at a screen value of 85lpi, nowadays 200lpi line screen elastomer plates are widely seen on the market. Back in the days, the low screening of the elastomer plates caused it to be used mainly for the printing of uncomplex repeating background designs on tissue, wallpaper and other materials for the decorative market. In general elastomer plates are more durable than photopolymer sleeve in terms of scratch resistance, heat resistance and the ability stand up to solvent inks. The longer production life eliminates the need to purchase more plates for long runs and repeated jobs.
At the end of the day, choose the plate according to what you would like to accomplish. There are many vendors on the market to choose from, choose your vendors wisely as the capability of different vendors may vary.
Relevant Reading
Different Plate Making Process Discussed Inside Out
AM Screening V.S FM Screening

Article by Daywey Chen, KYMC