Coating for Food Packaging
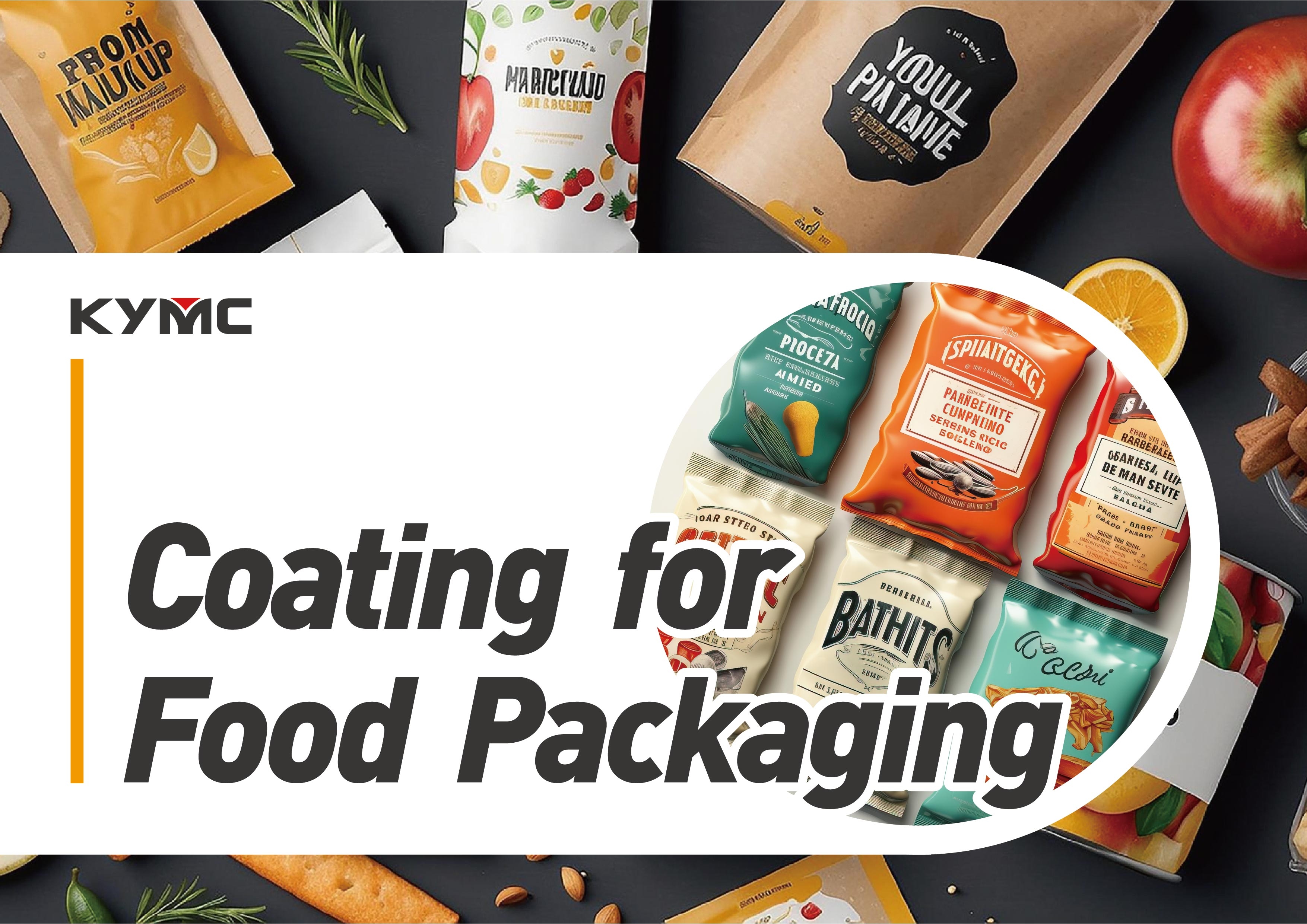
Keeping it fresh, containing the grease, controlling gas exchange, and preventing light penetration and aromas leaking are the main functional aspects of coating in food packaging. From an aesthetic perspective, coating helps the food to look as attractive as possible to the consumer. With the growing demand for convenient food due to the busy urban lifestyle, the need for preserving the food and marketing it to the consumers is also growing. According to Vantage Market Research, the food coating market is valued at USD 3.3 billion in 2022. It is projected that the food coating market will reach a value of USD 4.99 billion by 2030 at a CAGR of 6.12% between 2023 and 2030. So how does coating work, and what are the mainstream coatings on today’s market?
The coating is applied to the substrate usually through a roll-to-roll process, as it is the most efficient coating process for a mid to long-run job. Where rolls of the substrate are unwinded and go through the coating machine, where coating liquid is picked up by rollers. There are many different coating processes. Some of the main ones include direct gravure, reverse gravure coating, offset gravure coating, micro gravure, flexo coating, and four roller coating. The different coating methods are suitable for different coating viscosity. The different coating method allows for the delivery of different coating weights, coating speed and coating precision control. If you are looking for a higher coating weight, you can consider direct gravure or reverse gravure coating. If you are looking for a finer coating weight, you can consider offset gravure coating, flexo coating, and four roller coating. Among the different coating options, flexo coating provides the fastest coating machine speed.
The most used coating substance for food packaging is an epoxy-based resin. The epoxy-based coating is strong, flexible and provides good resistance. However, the drawback of Epoxy-based coating is the use of a chemical compound bisephol-A(BPA) during creation, which is linked to toxic effects in humans by disrupting the human endocrine system. Wax coating is also a commonly used coating for food packaging. Wax coating is prevalent in fast food packaging to prevent oil and grease from leaking. Nowadays there are biobased barrier coating solutions that are more environmentally friendly. Bio-based coatings can be made from a variety of bio-based materials, such as natural oils, resins, starches, cellulose, proteins, and other plant or animal-derived components. The different coating solutions have their pros and cons. They require different coating methods as they have different viscosity, and require different coating weights and coating precision. KYMC can deliver different coating methods, to work out an optimal process with our clients to optimize results.
Most of the time, coating is not the only process involved in creating food packaging. Keeping the food fresh is not enough. To appeal to the consumer is equally important. Therefore, printing is commonly done before or after the coating. When printing is done before coating, the coating protects the print and gives the print gloss. The coating can be applied to the whole substrate, or it can be applied only to the printed area (also referred to as insert coating). Insert printing requires a good registration press to complete the job. When printing is done after the coating. The coating helps to protect the food inside and prevents an exchange of substances (moisture, grease, gas) between the interior and exterior. KYMC provides hybrid presses that combine both the coating process and the printing process to maximize production efficiency. The coating and printing process can be completed in one pass to minimize job change and waste produced job change. At the same time, KYMC hybrid presses are great at bounce control and have excellent registrations making insert coating / printing precise.
As the coating for food packaging market is expected to rise in the future. It is a great time to capture this opportunity. With the right equipment for coating and printing, you can deliver efficient production. With KYMC’s hybrid press, the process can be optimized to work on various coating solutions that fulfill the market’s need.