What web tension should I run at on a roll to roll solution?
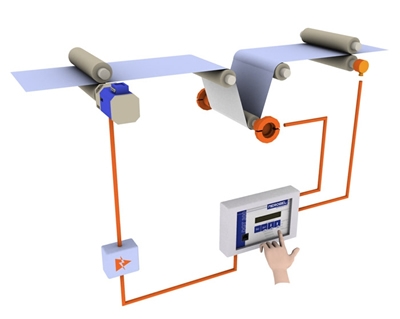
One of the greatest advantages of the roll to roll (R2R) printing and laminating solution is its production speed when compared to sheet feed solutions. These rolls of substrates allow the web to be fed continuously into the printing and laminating equipment and are then cut into the appropriate size after the printing and laminating are completed. This roll to roll process is very cost effective for large orders.
One of the main challenges of the roll to roll printing and coasting solution is to maintain a suitable and constant web tension. Tension must be controlled to the web to keep them in traction with the idle rollers and driven rollers. You want to put just the right amount of tension on the web, putting too much or too less can cause trouble either way.
When too much tension is applied
- Web stretch for film materials increasing the length of the web
- Web breaking when the tension applied exceeds the maximum tension that the material could withstand
- Web wrinkles can occur especially in laminating where the tension of the webs to be laminated is different
When too little tension is applied
- Slippage of the web on the rollers causing the misalignment of the web
- Loose webs causing printing registration issues
General guideline
According to TAPPI testing guide (Technical association of the pulp and paper industry) when controlling the web tension, a general guideline is to apply 5% ~ 25% of the maximum web strength, and around 0.5 ~ 1 PLI/mil of thickness.
Web tension control could be categorized into 3 main zones, unwind, internal and rewind. Each zone is independent therefore each zone could have its own tension. The torque required to provide a certain level of tension is measured by the total tension applied x the roll’s radius. Therefore, during production, the torque required at the unwinder will decrease as the roll diameter decreases and the torque required at the rewinder will increase with the increase in the roll diameter. The tension at the unwind and internal zones should remain constant throughout the production. However, this is not the case for the rewind zone. When the web is rewinded at the end of the production. As each layer builds up compressive forces which can cause the inner layer to wrinkle. Therefore, the tension reduces as the rolls build up. This process is called the Taper tension.
It is important to control the tension. Some of the equipment for measuring web tension on a roll to roll solution include load cell, at the dancing roller, the fish scale method at the unwind zone…
The roll to roll process is an efficient production method for large orders as long as one of its most important factor “tension” is being controlled effectively.
Relevant Reading
Should I use a motor or brake for web tension control?
Tension Control - The Types of Motor and Brakes
Article by Daywey Chen, KYMC