Eliminate the Dangers of Steel with TruPoint® Doctor Blades
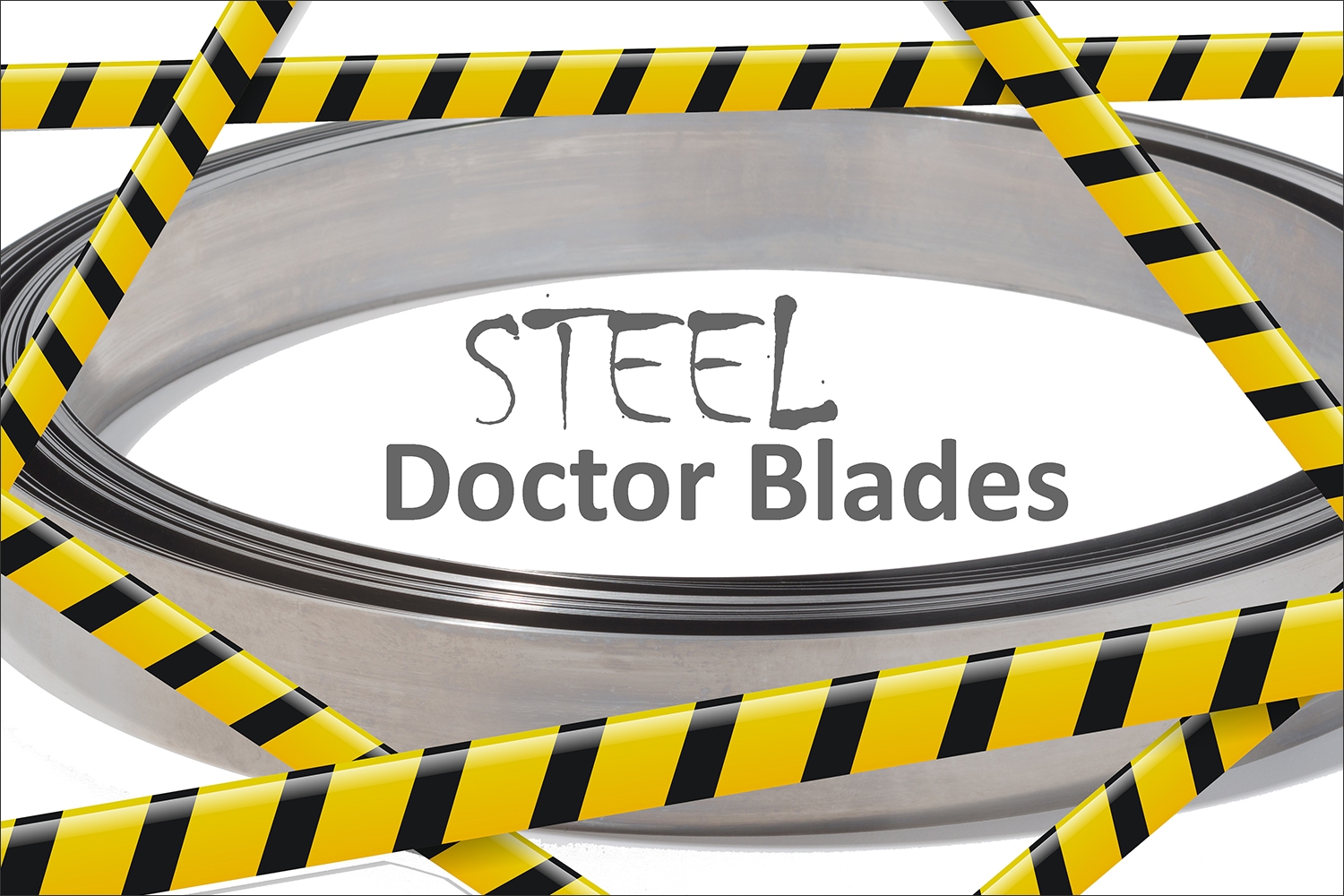
Every industry has its challenges, and for the flexo printing industry they include anilox scoring and pressroom injuries related to the use of steel doctor blades. Fortunately, due to advancements in polymer materials and tip designs, press operators no longer have to trade the safety benefits of plastic doctor blades for the effectiveness of steel. Today’s next generation TruPoint doctor blades deliver the best of both materials – longer anilox roll life, enhanced pressroom safety and superior metering performance.
Anilox Roll Scoring and Wear
The anilox roll has been referred to as the heart of the flexo printing press. It is responsible for transferring the precise amount of ink required to create an image exactly according to a customer’s specifications. If the roll’s surface becomes damaged, the defects will show in the printed image.
The most common types of anilox damage are scoring and wear caused by steel doctor blades. All doctor blades must be installed correctly to work properly. But installing a steel doctor blade at the wrong angle, backward or with too much pressure can cause small fragments of the metal blade to break away. The jagged pieces become lodged against the roll and cause a deep scratch or “score line” that destroys bands of anilox cells as the roll rotates.
Steel blades also accelerate wear across the surface of the anilox roller. Friction between the blade and roll erodes the anilox cell walls over time. As a result, the cell volume is reduced and the anilox can no longer carry the precise volume of ink that it was designed to transfer.
When an anilox roll becomes scored or worn, the damage is permanent and the roll has to be resurfaced or replaced. There is loss of material and productivity as well - discarded substrate, ink waste and press downtime - all at a significant cost to the printer.
Pressroom Injuries
Another downside of steel is that the material is responsible for a large number of pressroom injuries. A press operator is exposed to being cut anytime he’s handling steel blades – installing or removing them from the press, disposing them, and when changing end seals. The blades are especially dangerous when being replaced. Their edges become honed through contact with the anilox roll as they wear, leaving razor-sharp tips that can cause serious lacerations.
Workplace injuries are not only traumatic, but also have a significant effect on a company’s bottom line. Printers spend substantial amounts of money every year on workman’s compensation insurance and medical bills which come directly out of hard-earned profits. In addition, there are a variety of indirect costs that are harder to quantify but still impact earnings - lost productivity, work interruption, machine downtime, equipment repairs, training of replacement employees and accident investigation.
Solution: TruPoint Next Generation Polymer Doctor Blades
Flexo Concepts’ TruPoint polymer doctor blades provide smarter and safer alternatives in a wide range of flexo printing applications. All TruPoint blades are constructed from plastic materials that won’t damage the anilox roll or injure press operators. The materials don’t separate, splinter or crack and are inherently softer and less sharp than steel. Even when plastic blades are worn, their edges are not , enough to destroy a roll or cut a press operator.
TruPoint next generation doctor blades are engineered for printers who want to combine the best benefits of both plastic and steel in one blade. Unlike with traditional plastic materials, the TruPoint Orange® blade is constructed from an advanced polymer material that’s rigid enough to support a special MicroTip® edge. MicroTip is designed to achieve and maintain a fine contact area with the roll over the life of the blade. Orange is capable of metering line screens up to 785 L/cm as well as a steel blade and is a popular choice in flexible packaging, coating and label printing applications, where the blade also prevents UV ink spitting and start-up lines.
As graphics requirements grow in the corrugated printing sector, many printers are finding that standard UHMW cannot meter their mid-level line screen anilox rolls effectively. There is a “gap” between where UHMW is effective and steel is required on anilox line screens roughly between 120 and 200 L/cm. For printers who don’t want the safety and scoring risks of a steel blade, the TruPoint Green beveled doctor blade provides them with a good alternative. The material demonstrates better stiffness and twice the spring memory of standard UHMW, allowing it to maintain an effective contact area with the roll for the life of the blade. Green is an easy drop-in replacement for UHMW to enable printers to produce better print quality without resorting to a steel blade.
Printers, like people in other industries, struggle to find ways to reduce operational costs and improve safety. New polymer doctor blade innovations now give printers safer alternatives to steel blades that deliver the same level of quality. Choosing TruPoint next generation polymer doctor blades over steel is a simple way to prolong the life of anilox rolls, reduce lost-time accidents and deliver exceptional metering performance.