UV Ink Could Help Your Plant Save Up to 200K Annually
January 19, 2018 | Daywey Chen
2018-07-19
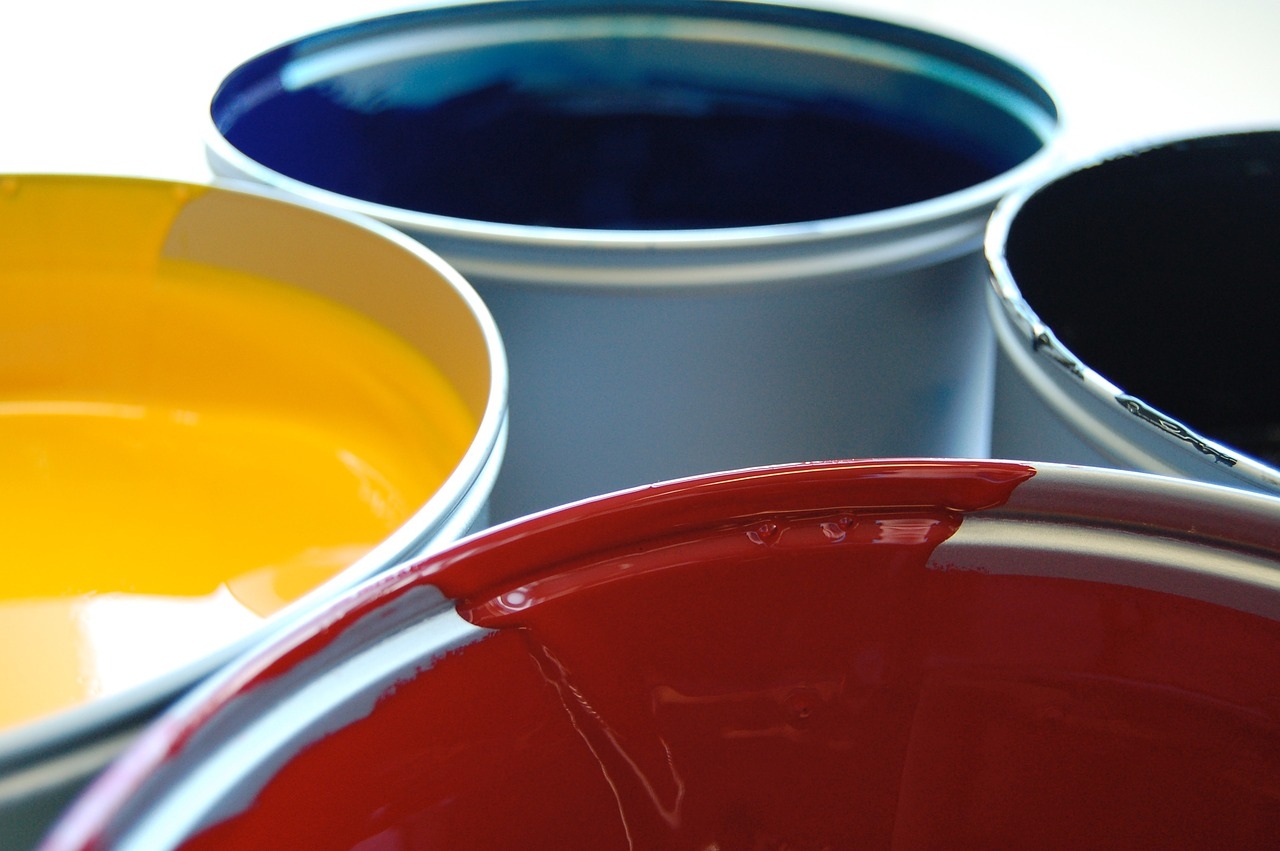
There are advantages and disadvantages to the different inks and their drying methods. Today we share a sample calculation of the economic advantage obtained from using UV inks and UV drying. The calculation assumes one print station, operating at one shift per day, five days per week and 52 weeks per year. The result gave us an estimated 164k in annual cost savings, and here is how we got to this number.
Ink Cost
UV inks cost approximately twice as much as water based inks. However, for UV inks, what you see is what you get since there are no evaporation involved. Allowing you to achieve the same result with much less ink when compared to the water based inks. Therefore, let’s consider a breakeven, no cost savings or extra cost are generated here.
Increased Production Hour
UV inks dry up only when exposed to UV light, therefore it could be left on the press on the ink pans overnight. This eliminate the need for setting up from scratch the next day and cleaning up after each run at the end of the day. Let’s estimate a saving of one hours per shift in job startup and shut down together, resulting in the following cost savings.
Savings:
(1 hr./day) x (5 days/week) x (52 weeks/yr.) = 260 hrs./yr.
260 hrs. x $300/hr. = $78,000/yr.
Scrap Reduction
UV ink is not evaporated during the printing process and stoppage and retain their color strength. This could reduce the amount of substrate wasted. Let’s estimate a cost of $0.14 per meter for LDPE film substrate at 45um with a 1300mm width. If we save 100 meters of film for every job, this will lead to a $14 in cost savings per job.
Savings
(2 jobs/day) x (5 days/week) x (52 weeks/yr.) x ($14.00/job) = $7,280/yr.
Reduced Washup
UV ink does not dry up but only polymerizes during exposure. This reduce the number of washup needed. Assuming each washup requires 0.5 hour and we could reduce one wash up per shift each day.
Savings
(0.5 hr./day) x (5 day/week) x (52 week/yr.) = 130 hrs.
130 hrs. x $300/hr. = $39,000/year
Increase Run Speed
Printing speed could increase when using UV inks due to the better drying capabilities of the UV curing process. Assuming we could increase the press speed from 250 meter/min to 300 meter/min, a 20% speed increase, while, averaging a revenue of $300/hr. Running the machine 20% faster could increase revenue by $60/ hour. Let’s say our machine is up 60 % of the time.
Additional Revenue
(8 hrs./day) x (5 days/week) x (52 weeks/ yr.) x (60%uptime) x ($60 /hr.) = $74,880/ year
Source :https://www.americanultraviolet.com/documents/Why_Use_UV_for_Web_Printing.pdf

Article by Daywey Chen, KYMC
Ink Cost
UV inks cost approximately twice as much as water based inks. However, for UV inks, what you see is what you get since there are no evaporation involved. Allowing you to achieve the same result with much less ink when compared to the water based inks. Therefore, let’s consider a breakeven, no cost savings or extra cost are generated here.
Increased Production Hour
UV inks dry up only when exposed to UV light, therefore it could be left on the press on the ink pans overnight. This eliminate the need for setting up from scratch the next day and cleaning up after each run at the end of the day. Let’s estimate a saving of one hours per shift in job startup and shut down together, resulting in the following cost savings.
Savings:
(1 hr./day) x (5 days/week) x (52 weeks/yr.) = 260 hrs./yr.
260 hrs. x $300/hr. = $78,000/yr.
Scrap Reduction
UV ink is not evaporated during the printing process and stoppage and retain their color strength. This could reduce the amount of substrate wasted. Let’s estimate a cost of $0.14 per meter for LDPE film substrate at 45um with a 1300mm width. If we save 100 meters of film for every job, this will lead to a $14 in cost savings per job.
Savings
(2 jobs/day) x (5 days/week) x (52 weeks/yr.) x ($14.00/job) = $7,280/yr.
Reduced Washup
UV ink does not dry up but only polymerizes during exposure. This reduce the number of washup needed. Assuming each washup requires 0.5 hour and we could reduce one wash up per shift each day.
Savings
(0.5 hr./day) x (5 day/week) x (52 week/yr.) = 130 hrs.
130 hrs. x $300/hr. = $39,000/year
Increase Run Speed
Printing speed could increase when using UV inks due to the better drying capabilities of the UV curing process. Assuming we could increase the press speed from 250 meter/min to 300 meter/min, a 20% speed increase, while, averaging a revenue of $300/hr. Running the machine 20% faster could increase revenue by $60/ hour. Let’s say our machine is up 60 % of the time.
Additional Revenue
(8 hrs./day) x (5 days/week) x (52 weeks/ yr.) x (60%uptime) x ($60 /hr.) = $74,880/ year
Possible Annual Cost Savings (USD) |
|
Ink Cost | $0 |
Increased production hour | $78,000 |
Scrape reduction | $7,280 |
Reduced washup | $39,000 |
Increase run speed | $74,880 |
Total | $164,060 |
Source :https://www.americanultraviolet.com/documents/Why_Use_UV_for_Web_Printing.pdf

Article by Daywey Chen, KYMC