The adoption of Industry 4.0 projects could lead to a 30% to 50 % reduction machine downtime.
December 8, 2017 | Ivan Lin
2018-07-19
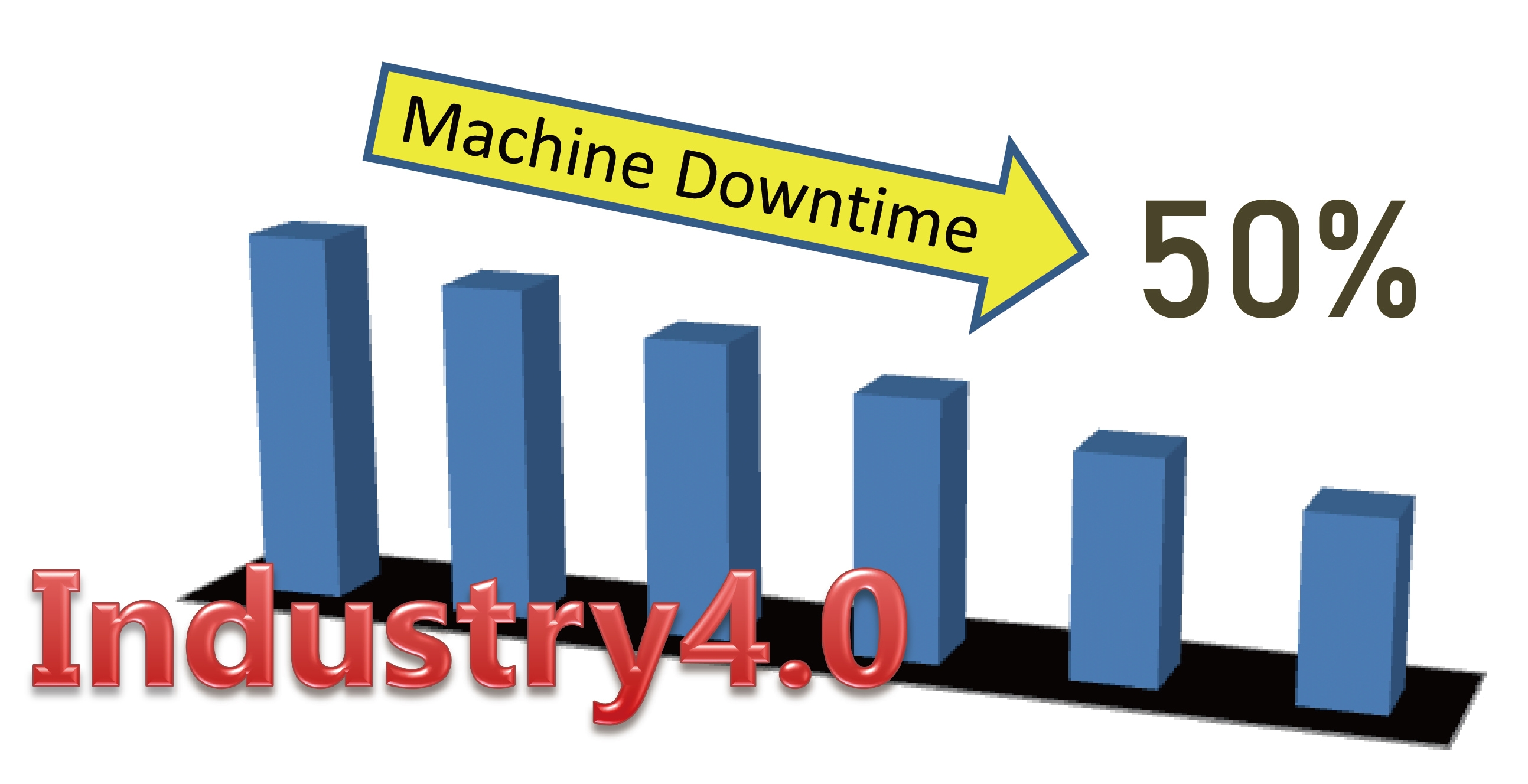
In the internet era, more and more hardware devices are connecting to the web. Different devices are communicating with each other and with different management platforms to form the internet of things. In the printing and converting industry, one of the Industry 4.0 ideas is the communication between the different parts of the printing and converting process, enabling companies to utilize the information gathered to produce valuable actionable items in its production process, customer services, inventory management, and supplier management. According to a research byMckinsey&Company, the adoption of Industry 4.0 projects could lead to a 30% to 50 % reduction in machine downtime.
Today we share with you an Industry 4.0 project example from a packaging company that mainly produces bags for food services, retail, and grocery industries.
Before the implementation of the industry 4.0 project, production job orders are planned out by the production planning department, with each job order printed out and listed on a board for reference. The details of each job order are also printed out and placed into folders to be situated next to each printing machines so the operator knows his next task on the machine. This sometimes could lead to human errors in the misalignment between job order and the machines during folder filing. After the adoption of the Industry 4.0 project, the job order details could now be sent directly to the machines from the company management system. The operator could cross-reference the physical documentation and the job task displayed on the machine for confirmation, therefore minimizing fault. As shown in Figure 1, each job task number is listed along with information such as print design sample, plate number, number of rolls printed and to be printed, the repeat length, the color of the substrate, the thickness (gauge) of the substrate and the color to use at each printing station. The end result is a reduction of error tasks performed that lead to a reduction in downtime.
Figure 1

Another implemented feature during the project is the real time monitoring of the production process as shown in Figure 2. Each machines performance could be recorded, including running speed of the machine at different time, total feet ran, rolls printed and rolls to be printed. The information is passed onto management systems for the management staff to review. The data collected allows management to understand the productivity during the different shifts. This in turn became an incentive for operators to be more productive, meaning running the machine at high line speed and with less downtime, since his performance is now monitored by management all the time. Good performance could then be rewarded accordingly. Furthermore, any machine downtime could be alerted to the management at the different levels in real time. As result, this will reduce the problem solving time and machine downtime.
Figure 2
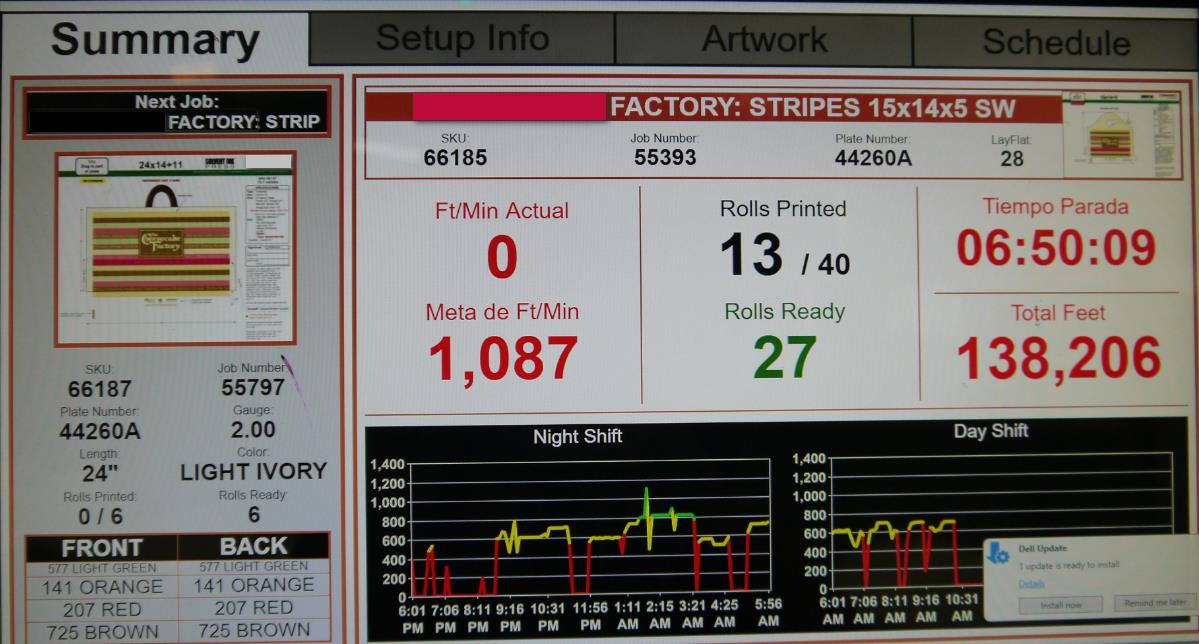
Technology advancement allows data to be collected at real time and at massive scale. It is crucial for businesses to turn these data into knowledge and actionable items to remain competitive in today’s competitive environment. The successful usage of the data could reduce production downtime and increase productivity.
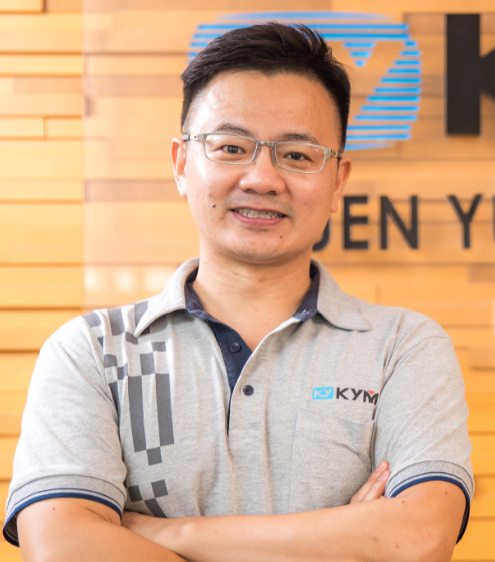
Contributed by Ivan Lin, KYMC
Today we share with you an Industry 4.0 project example from a packaging company that mainly produces bags for food services, retail, and grocery industries.
Before the implementation of the industry 4.0 project, production job orders are planned out by the production planning department, with each job order printed out and listed on a board for reference. The details of each job order are also printed out and placed into folders to be situated next to each printing machines so the operator knows his next task on the machine. This sometimes could lead to human errors in the misalignment between job order and the machines during folder filing. After the adoption of the Industry 4.0 project, the job order details could now be sent directly to the machines from the company management system. The operator could cross-reference the physical documentation and the job task displayed on the machine for confirmation, therefore minimizing fault. As shown in Figure 1, each job task number is listed along with information such as print design sample, plate number, number of rolls printed and to be printed, the repeat length, the color of the substrate, the thickness (gauge) of the substrate and the color to use at each printing station. The end result is a reduction of error tasks performed that lead to a reduction in downtime.
Figure 1

Another implemented feature during the project is the real time monitoring of the production process as shown in Figure 2. Each machines performance could be recorded, including running speed of the machine at different time, total feet ran, rolls printed and rolls to be printed. The information is passed onto management systems for the management staff to review. The data collected allows management to understand the productivity during the different shifts. This in turn became an incentive for operators to be more productive, meaning running the machine at high line speed and with less downtime, since his performance is now monitored by management all the time. Good performance could then be rewarded accordingly. Furthermore, any machine downtime could be alerted to the management at the different levels in real time. As result, this will reduce the problem solving time and machine downtime.
Figure 2
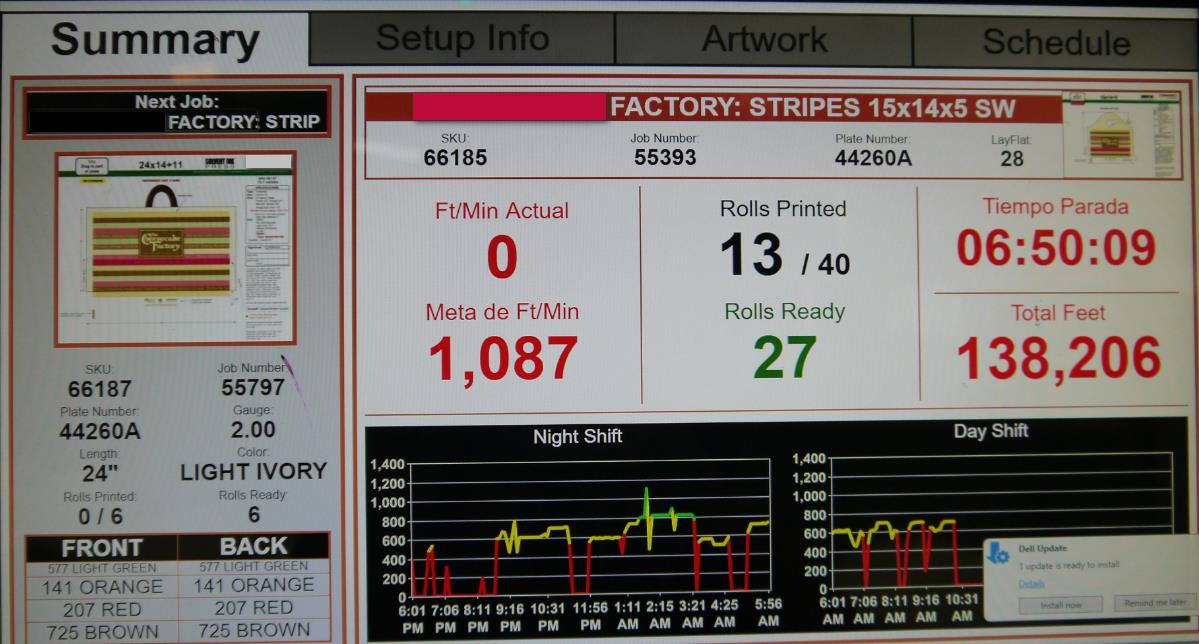
Technology advancement allows data to be collected at real time and at massive scale. It is crucial for businesses to turn these data into knowledge and actionable items to remain competitive in today’s competitive environment. The successful usage of the data could reduce production downtime and increase productivity.
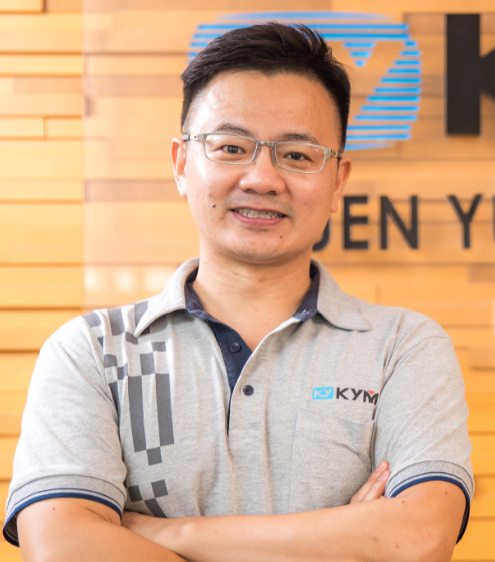
Contributed by Ivan Lin, KYMC